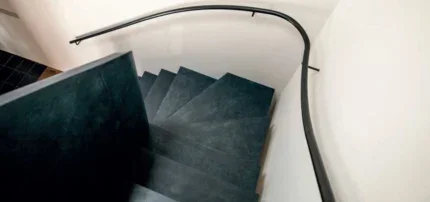
A “remarkable” retrofit of Brighton’s timber-framed landmark arts centre by Feilden Clegg Bradley Studios, the Brighton Dome Corn Exchange & Studio Theatre was named the UK’s best timber building in a ceremony at Carpenters Hall in late November – winning the Gold Award at the 2024 Wood Awards.
The project, which won out over more than 150 buildings in the UK to claim Gold, was a triple winner, as in addition it took the awards for both the Restoration & Reuse, and Structural categories.
Set within historic Regency gardens and adjoining the famous Royal Pavilion, the Grade-I listed Corn Exchange and Grade-II listed Studio Theatre buildings have been thoroughly restored, strengthened and remodelled – revealing a rich timber heritage to visitors.
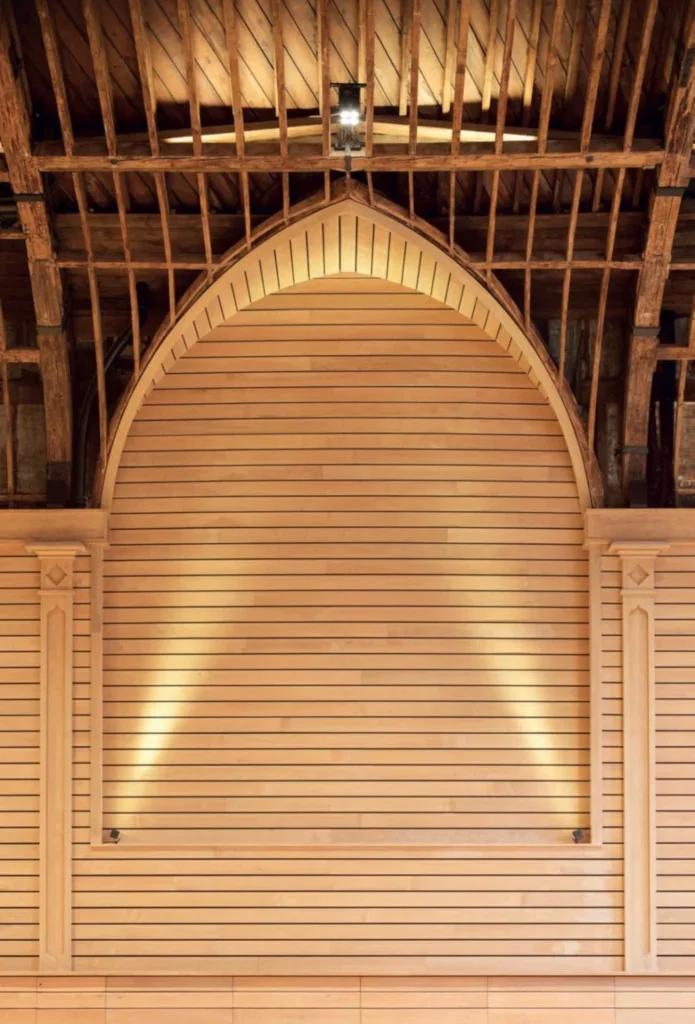
As well as improving connection and accessibility with the introduction of a new foyer space and café, the project has seen the careful repair and restoration of the UK’s longest single-span timber frame through phenomenal effort and incredible engineering by the project team.
By re-analysing the whole structure, meticulously understanding every joint and size, the project team brought the building up to modern design standards with a solution that preserves and enhances the original timber roof – repairing rather than replacing damaged parts.
Through the matching of old timber with new, the team has created a stunning space with an inherent warmth in its colour, which acts as an ode to the UK’s timber heritage.
The construction for Brighton Dome Corn Exchange & Studio Theatre was completed by R Durtnell & Sons and Westridge Construction Ltd, with wood supplied by Neil Burke Joinery and Weitzer Parkett. The structural engineers were Arup and the building services and sustainability consultants were Max Fordham.
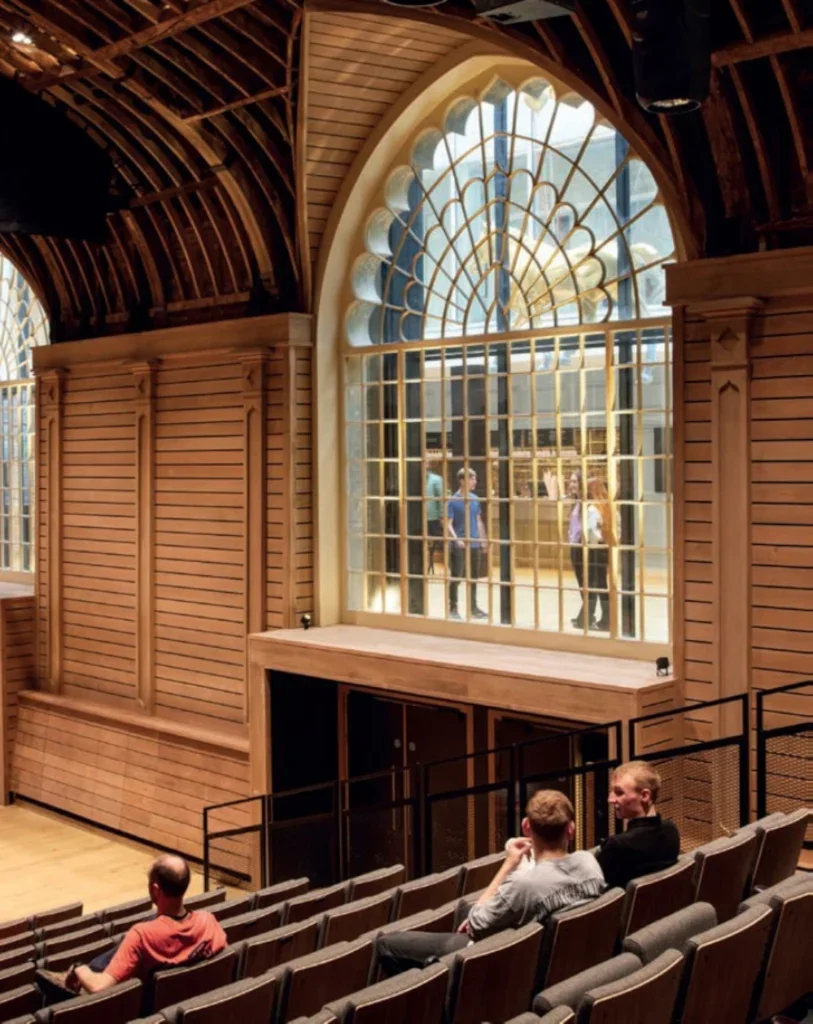
“This project highlights two important criteria for the Wood Awards,” said Jim Greaves, lead judge of the Wood Awards and principal of Hopkins Architects.
“Firstly, it has retained and carefully restored an historic structure and secondly, the new work has been sensitively designed to fit within it. This team has put heart and soul into this endeavour, and we are happy to recognise that,” said Mr Greaves.
“Every aspect of design has been considered within the interior of this building,” he added. “The historic roof, stripped bare, sits atop a newly restored interior that recalls the earlier use of the building as a riding school. A space that historically was given over to the horses is now given over to the public.
“The Brighton Dome Corn Exchange & Studio Theatre stands as an excellent example of restoration and reuse which we can all learn from. The building demonstrates that advanced engineering and skilled craftsmanship allied with a sensitive approach to design can deliver a newly restored and repurposed building fit for the 21st century.”
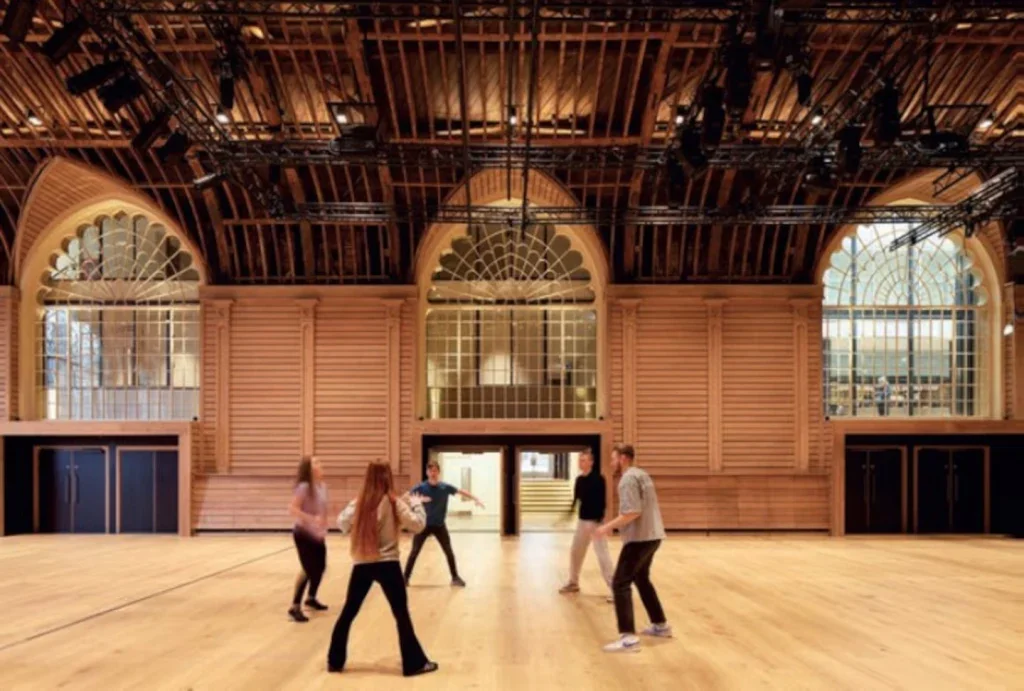
The Wood Awards building judges, a team of world-leading professionals, visited all 18 buildings shortlisted in the Wood Awards before deciding the winner, in one of the UK’s most rigorous assessments for any competition.
“Congratulations to the team behind the Brighton Dome Corn Exchange & Studio Theatre, and all entrants in this year’s Wood Awards,” said David Hopkins, CEO of Timber Development UK (organisers of the Wood Awards).
“Timber – and retrofit – have crucial roles in decarbonising construction, and as an organisation we spend a lot of time campaigning, promoting and educating about the role of timber. But there is no substitute for showing examples in practice.
“All of the winners and the shortlisted projects are incredible examples of British architecture and design, and I know the judging gets more difficult every year – with so many wonderful timber buildings in the UK continuing to emerge,” said Mr Hopkins.
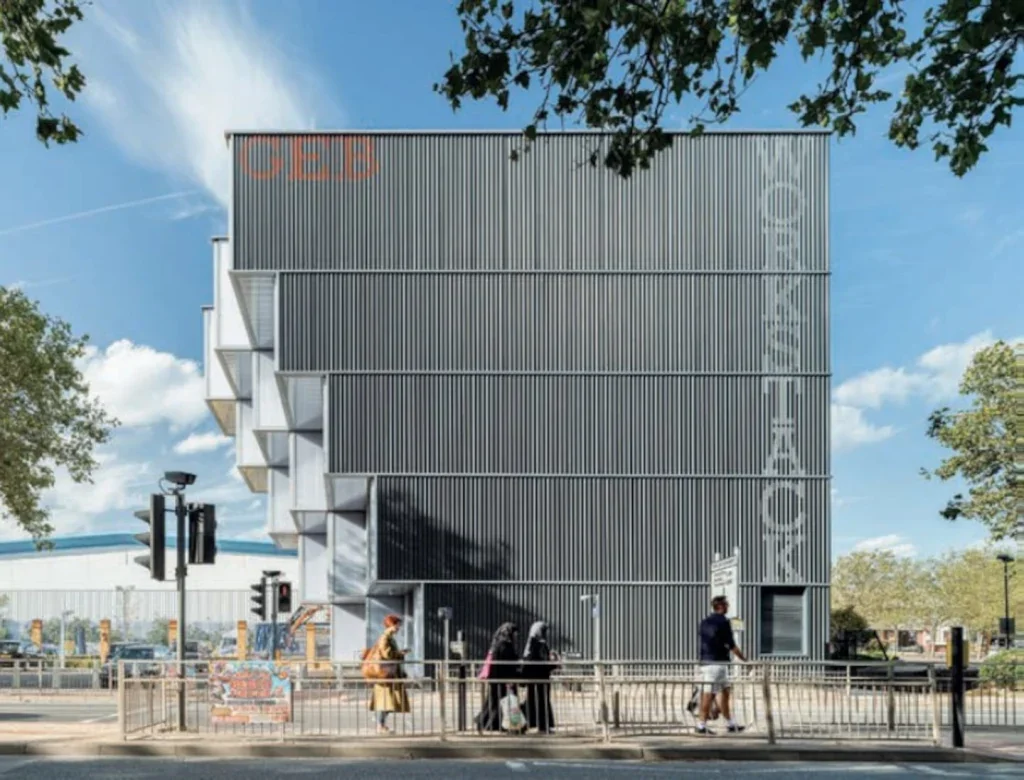
“We are seeing climate conscious architects, engineers, and other designers increasingly choosing to use wood as the primary material in their projects – recognising its low-carbon nature, warmth, and beauty – which has so brilliantly been put on display this year.
“Every single one of the entrants were remarkable, and we hope that the 2024 awards will inspire even more designers to work with wood.”
WINNERS IN OTHER CATEGORIES
This year’s event celebrated 14 awards and recognised 11 highly commended projects across the Buildings and Furniture & Product categories.
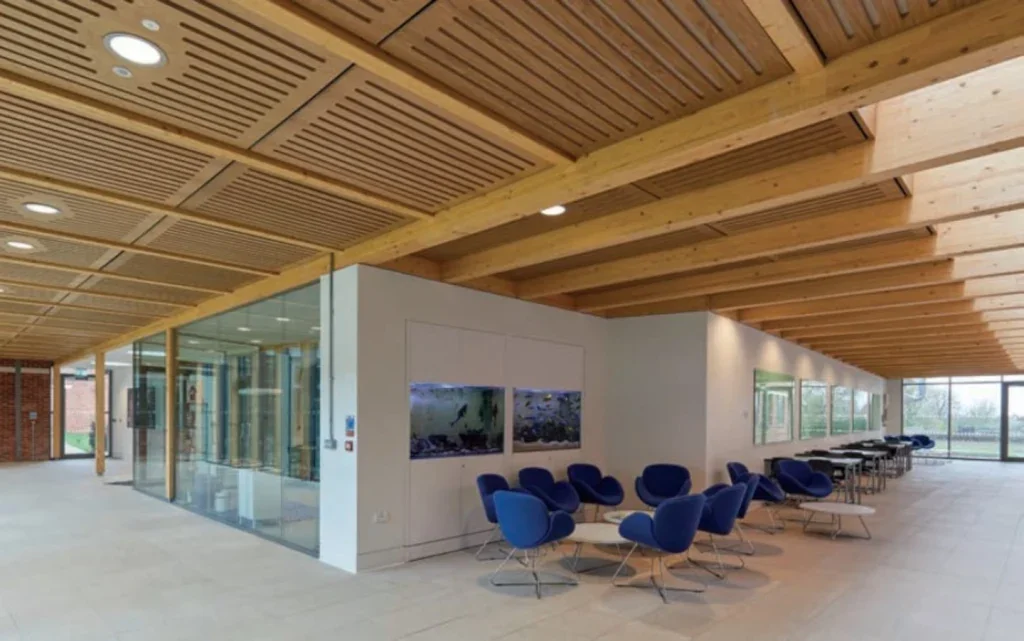
The winner of the Commercial and Leisure category was dRMM’s Workstack in Greenwich, London (TTJ July/August 2024).
Primarily constructed from engineered mass timber, WorkStack’s distinctive cantilevered form makes maximum use of a small footprint, providing 14 variably sized workshop units over five floors. Taking inspiration from a ‘logstack’, the progressive overhang works as both solar shading and a covered delivery area.
With each building element designed to be as efficient as possible, the engineered mass timber structure uses limited steel, polycarbonate, glass and rubber only where function or regulation demands. By exposing the load-bearing timber walls and ceilings, the need for additional internal finishes was eliminated, reducing associated material resources and environmental impacts while offering biophilic benefits to users.
The timber species used included spruce CLT and glulam (Sweden, Austria, Germany), birch and spruce plywood (Finland) supplied by Hasslacher and Stora Enso. The offsite construction specialist was B&K Structures.
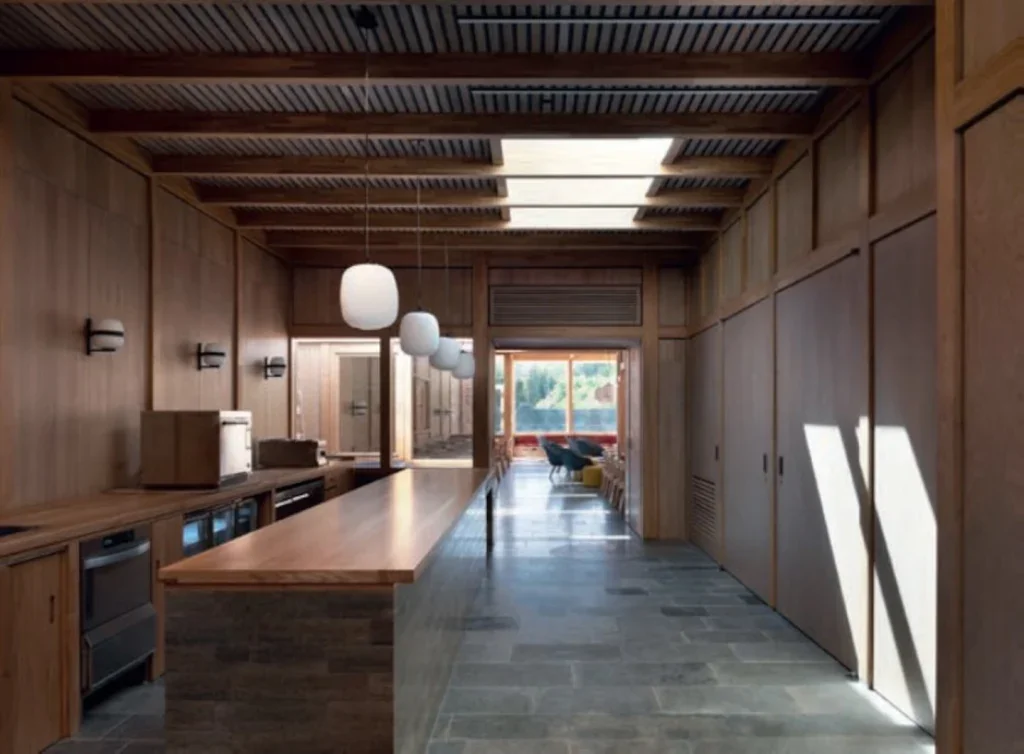
B&K Structures was also involved as CLT subcontractor with the Sustainability category-winning project – Haileybury SciTech – a new science and technology campus for Haileybury, in Hertford, that reimagines the way science can be taught in schools in the future.
The design, by Hopkins Architects, integrates a new CLT and glulam-framed extension with existing buildings, arranged around a central courtyard and cloister. The school’s existing 1934 Grade II listed Herbert Baker building has been carefully opened up at the rear to create an axial connection between one side of the cloister and the more recent 1990s Design Technology building opposite. This architectural move not only showcases SciTech but also consolidates the existing buildings to create a coherent overall campus.
The new elements of the project comprise a three-storey Teaching Building arranged in a linear block, and a two-storey Research Building, which is already home to several pioneering research projects, including the prestigious Stan-X project.
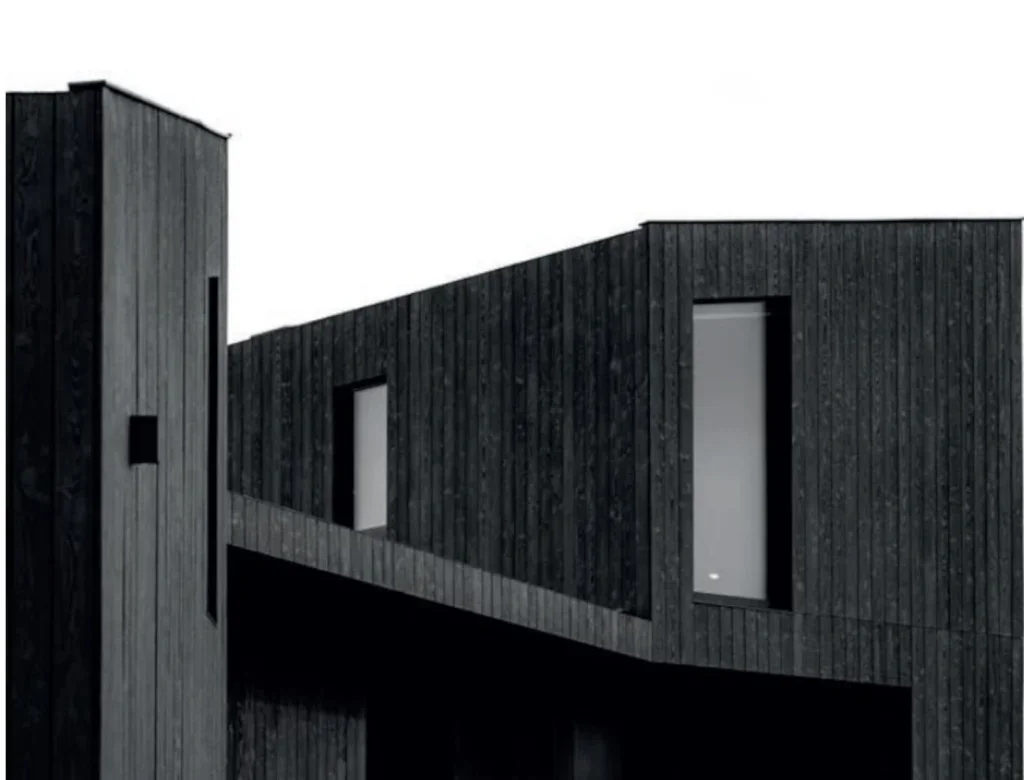
Haileybury SciTech fully embraces the aesthetics of timber, with CLT slabs left exposed throughout, utilising its structural and thermal properties. In addition, the use of CLT has substantially reduced the project’s embodied carbon by up to 56% per m2 compared to conventional structural methods.
The CLT engineer was Engenuiti and the wood – including spruce CLT (Austria), spruce glulam (Germany), and American white oak – was supplied by B&K Structures, Hanson & Beards, and UKA Systems.
Another seat of learning, Clare College was the worthy winner of the Education & Public Sector category.
Combining cutting-edge technology and traditional craftsmanship, the new River Wing at Clare College is an oak-framed extension to Cambridge’s second-oldest college.
The new wing complements and updates the existing court building by providing improved walkways, galleries, a lift and staircase, along with a riverside café for students and faculty.
Rising from a narrow wedge of land between the Old Court building and its neighbouring Trinity College, the River Wing is a masterpiece in skilful design and off-site manufacturing. The intricate oak glulam structural frame makes maximum use of all available space and daylight, while CLT is used for the floors and a three-storey lift shaft. To streamline installation on such a constrained site, large timber elements were preassembled in a factory before being precisely pieced together on-site.
The building’s beautiful finish is a testament to significant design detailing and co-ordination, including the creation of 525 individual structural connection details. Timber connections draw on traditional carpentry joints, such as dovetails and mortices, resulting in a startlingly low amount of steelwork.
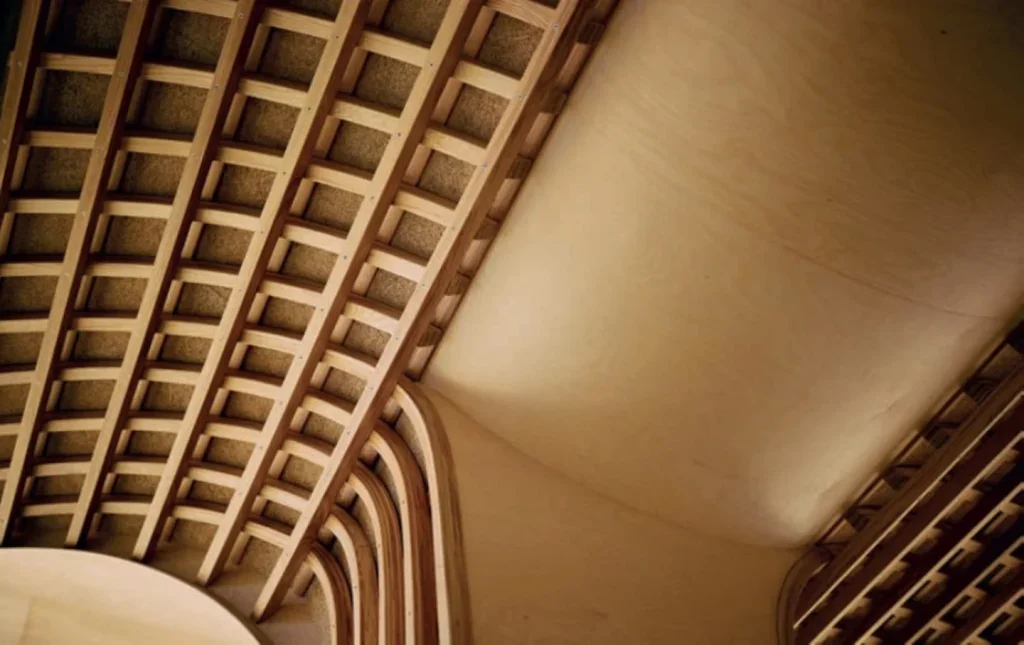
The timber species used were European oak (France, Croatia) and European spruce (Austria) and were supplied by Constructional Timber (Manufacturers) Ltd, who were responsible for construction of the structural frame. The architect was Witherford Watson Mann and the structural engineer was Smith and Wallwork.
There was a distinct Celtic flavour to the Research & Innovation award winner, which was Uist House.
Perfectly designed for its dramatic Outer Hebridean climate, this sculptural modular home overlooking a tidal lagoon fed by the North Atlantic Ocean, has been built from home-grown Welsh timber – specifically Welsh Douglas fir. Other species used included Sitka spruce (UK), larch (UK), and oak.
Constructed primarily in a factory in Wales, the house was shipped in seven prefabricated modules, travelling 570 miles across land and sea, to its final destination on the island of North Uist, where it was assembled.
Passive house levels of airtightness and insulation are combined with an equally uncompromising approach to embodied carbon. Bespoke timber box beams filled with cellulose insulation form a strong primary structure that can withstand the location’s extreme wind loads at a low carbon cost.
The contractor was Unnos Systems, which also supplied the timber. The IRO cladding and decking was from BSW Timber and the architect was Koto Design and Hiraeth Architecture.
Rhodes House Garden Pavilion scooped the Small Project award.
Set within the gardens of the Grade IIlisted Rhodes House, in Oxford, this new multi-purpose building forms part of a recently completed scheme that has modernised, refurbished and extended the 100-year-old headquarters of Rhodes Trust educational charity.
Harnessing traditional woodworking techniques and modern engineering, the timber lattice that forms the structure of the pavilion cantilevers over the root protection area of nearby trees. A green roof sits on top of the sweeping timber structure, which itself rests on frameless load-bearing glass walls.
Using parametric modelling and detailed analysis, the roof geometry has been tailored to optimise aesthetics, structural efficiency, acoustic performance and curvature limitations – resulting in a breathtaking feat of timber design.
The timber used was spruce LVL from Scandinavia, and European ash and was supplied by Braden Timber Structures, which was also responsible for the joinery (along with Paragon Joinery for the internal joinery).
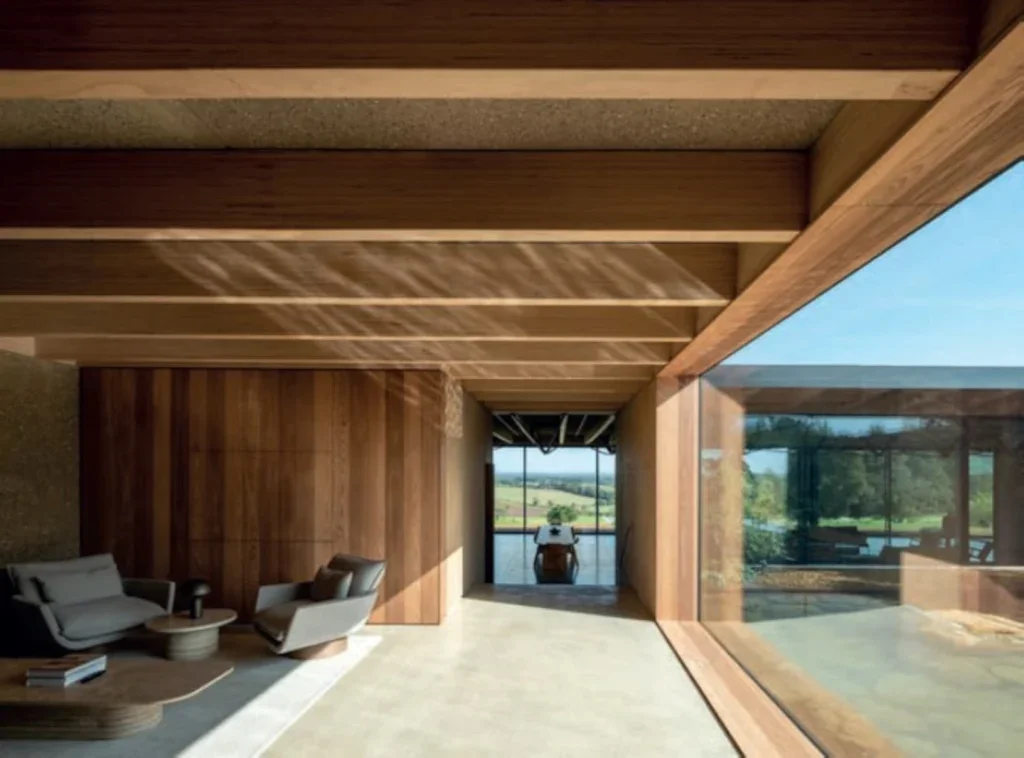
HIAVEN – a contemporary farmhouse at the centre of a regeneration project that breathes new life into a previously derelict Cotswold farm – was the winner of the Private category.
Sitting amidst 100 acres of farmland, which has been newly planted with trees and wildflowers, this low-energy building has been designed to be visually seamless and integrated within its surrounding landscape.
Using a minimal material palette of timber and acid-etched concrete, the new farmhouse provides living accommodation and exhibition space, including a vast 12×36m column-free area.
Characterised by an entirely exposed structure, the project is a showcase of hybrid engineering as architectural design. The key unifying element of the structure is the innovative timber-concrete composite roof. Here, LVL roof beams have been combined with precast concrete planks to create an efficient and elegant roof solution with inherent thermal mass, designed to be easily demounted and reused.
Pollmeier supplied the beech LVL, the architect was BPN Architects and the timber draughting was the responsibility of Redgate Engineering Ltd.
Bough Terrace in London secured victory in the Interiors category.
Celebrating timber in colour, texture, age, form, function and structure, this project transforms a Victorian townhouse and reveals intriguing insights into the building’s history.
With a commitment to retain as much of the existing timber lattice interior structure as possible, the house has been stripped back to its bare bones, revealing the tactile character and imperfections of its timber floor joists and roof trusses.
Throughout, the existing gnarled and textural timber structure has been married with new solid timber, which by contrast is sharp and precise. A singular trunk-like post on the lower-ground floor stems upwards and outwards, with new and old wood extending through the layers of the house like branches, culminating in a plywood canopy on the top ceiling.
Built by bespoke shipbuilders, a curved staircase has been made from hand-folded plywood and stained midnight blue. Cleverly hiding its fixtures, the stair seems to levitate, creating a dramatic and ethereal transition to the upper floor, where dark roof trusses contrast strikingly with the ply ceiling.
The wood supplier was Elliotts and the species used were redwood pine (Sweden and Finland), Douglas fir and reclaimed timber. The joinery elements were carried out by Cube and the architect was Tuckey Design Studio.
FURNITURE & PRODUCT AWARDS
Among the furniture and product design pieces that won their categories were: Communion, which won the Bespoke category; Ebworth Stools, which won the Production category; Karl and Rita, winners of the Student Designer category; and Endless Orbit, which triumphed in the Sculptured Object category (see p5).