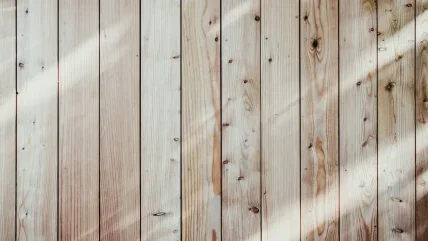
David Hopkins Timber Development UK chief executive
As we head into 2024, most of the timber trade will just be pleased to see the back of 2023 rather than being overly optimistic about the year ahead.
A huge slowdown in housebuilding and renovations along with increased business costs left a lot of members aiming for survival rather than success.
In some ways 2024 looks to add more of the same, though there are a few glimmers of light in the darkness.
The immediate outlook for UK construction is not great: the CPA forecasts private housing starts to fall by 11% largely as a continuing result of the steep rise in mortgage rates since the Liz Truss economic bombshell in autumn 2022, coupled with continued inflation and falling real wages.
The removal of Help to Buy as an incentive for first time buyers has also aggravated the situation, showing the importance of policy stability for our sector.
Here though we could be in for further changes, with a general election coming some time in 2024.
In some ways this could look like the last thing we need. We’ve had 16 housing ministers and counting from the Conservative government, plus numerous general elections in the past eight years – the biggest period of directionless churn and instability I have ever witnessed in British politics.
This time though, the contest looks tighter, which should help focus policy offerings in the real world for a change, and housing is firmly on the agenda for both parties, along with a major focus on sustainability and low-carbon development.
Both of these themes have converged in the Timber in Construction Roadmap, which was launched late last year. The roadmap was developed in response to calls to decarbonise construction and to increase UK forest cover and concluded that increasing timber in construction would be an ideal way to achieve both goals. It could lower the embodied carbon of the built environment, while providing a market-led pathway toward more planting.
The report looks at a variety of barriers to overcome, as well as opportunities to increase timber usage. Timber Development UK, along with key partners such as Confor and the Structural Timber Association, have been actively involved in the development of this report, bringing the full supply chain together. It is a great opportunity to increase market share, even if the market is in dire straits.
There will be a lot of work to do – to educate the market, increase the value proposition of home-grown timber, gain greater dialogue with insurers and developers – and we have already started making progress against all of the themes in the report.
We have also made sure that the report does not get buried or seen only as a government initiative to be ditched by the opposition. Our All-Party Parliamentary Group autumn lunch used this report as its main focus in November, and even welcomed former forestry minister Trudy Harrison (who led the development of the roadmap) as a co-chair, making it a truly cross-party affair.
With the help of our members, we will be publicising this to current and incoming policy makers of all parties, showcasing the importance of our sector in social, environmental and economic terms.
Inflation is already easing and, as we move through the year, we should see interest and mortgage rates improving, providing better conditions for the housing market. We want to make sure that, as the market returns, we can use this renewed interest in timber to take a greater building materials share for our members.
Alastair Kerr, Wood Panel Industries Federation director-general
Demand for wood panels remained relatively buoyant through most of 2023, albeit there has been a steady realignment back to pre-Covid trends. The additional headwind created by the war in Ukraine has driven an increase of imports from mainland Europe, which has put pressure on prices. German energy policy, combined with rental caps has had a dramatic impact on the demand within Germany, forcing suppliers to look to other markets. There have been increases of up to 20% in imports to the UK of MDF and OSB. Particleboard imports have also increased but to a lesser degree. There is unlikely to be a significant change in the depressed European markets through 2024 and maybe beyond, so we expect a continuation of inflated imports.
Whilst UK inflation rates have been falling, further drops are likely to be slow in coming through and this will be to the detriment of mortgage holders who won’t see any quick relief. Those who are coming off fixed rate mortgages will be particularly impacted. New residential housing starts were slowing in Q3 2023, and we expect this trend to continue into 2024, at least until inflation stabilises and some confidence comes back into the economy.
Whilst all market segments are under pressure, some are performing better than others. Repair, maintenance and refurbishment is holding up, as is social housing, commercial interiors and student accommodation. Retail sales of furniture are being hit as consumers rein back spending and at the same time imports of cheaper furniture items are increasing. This could potentially lead to some consolidation, particularly amongst the smaller downstream domestic furniture processors.
House building is key to both construction board sales and furniture and as such, the Construction Products Association forecast of no growth in domestic housing in 2024 suggests that ‘lean times’, will continue well into 2024. Whilst unexpected bounce backs can happen, particularly on the run up to an election, there are some fundamentals which will act as a break on any rapid increase in new housing and construction. Of particular concern is the lack of skilled trades people following rule changes after Brexit. If new rules on work visa’s being discussed presently go through, this will only exacerbate the problem.
On the bright side, the recognition of the benefits of timber and wood products in construction is gaining momentum and timber frame should be a significant beneficiary as builders and developers, particularly in England, take on more frame developments. The longer-term outlook for panels generally, but particularly OSB, is bright.
The panel industry in the UK and Ireland has a history of resilience in challenging times and this current downturn is no different. Operating in mature markets, particleboard and MDF have seen significant investment into value adding over the past decade and this has helped to diversify the offering and expand the market opportunities.
Danny Catherall, Timber Connection managing director
After the highs and lows of the last couple of years due to the pandemic, some much needed stability in the hardwood trade would be much appreciated for 2024.
For many, the last couple of years, when averaged out, may have been more profitable than pre-pandemic levels, but the extreme trading conditions that came with it will not be missed. It appears however, that we in the hardwood industry are not out of the woods just yet. The trade continues to see weakness in certain sectors of the supply chain that reacted to inflationary price increases later than others and are now realigning prices down until they find their level again.
Timber Connection has always remained positive irrespective of the trading conditions it has faced over the years and we will continue to ensure we are market leaders in that respect. Our commitment to ensuring we have enough timber in the pipeline allows our customers to rely on us at any point in their purchasing process. The importer/merchant customer base that is the backbone of our DNA remains able to buy from Timber Connection in the way that suits them, from forward purchasing direct from source, to buying containers ex-ship/ex-quay, or arranging call off programmes from stock to buying packs on a just-in-time basis from our 300,000ft2 warehouse operation in the north-west.
We are hopeful, despite the continued gloomy economic forecast, that this will be the year that puts us and our customers on a steady upward growth curve we experienced pre-Covid. There will be no time for complacency as we continue to future proof the company, ensuring we have the expertise together with the willingness to change with the times. Embracing customers preferences to interact at different levels, from simply talking to them, to providing them with the possibilities that digitalisation offers, with e-commerce at the front of our activities in today’s fast and ever-changing trading environment.
Dave Chapman, BSW sales director
The only thing certain about the market for 2024 is the uncertainty.
Looking back at 2023, it’s been a year of two halves. Quarter one was reasonable and quarter two saw balanced demand in all sectors. That said, some customers have exceeded purchases from 2022, which is a great performance given the difficulties in the current market. However, more widely in the latter six months, prices have come under pressure.
Given the effect of increased costs of wages, transport and importantly log costs both here and in Europe and Scandinavia, it’s almost incomprehensible that in some cases, some sectors are expecting to pay levels seen several years ago.
In terms of import pricing where the production cost pressures are equally as significant, the magnitude of the fall has been surprising. At the height of Covid shortages, C24 was up to €600/m3 – we are now seeing prices well below this level.
The main factor behind this is depressed demand and people’s requirement to turn stock into cash. Businesses don’t want high volumes bought at higher than current market prices sitting on their inventory as demand in Q4 reduces.
We are seeing a further consolidation in all sectors and this is expected to continue next year and we will undoubtedly see some merchants close as a result.
Another concern, as we experienced in the 2007-2008 downturn, is that credit cover starts to reduce restricting a company’s ability to trade and a supplier’s ability to supply material.
I think we’re reaching the bottom on price and will be under huge pressure in Q1 this year to increase pricing, given the continued challenges on products and log costs. Certainly, we should see some movement in import pricing as the US market begins to perform again.
In 2024 you’ve got a massive amount of uncertainty. You have the cost-of-living crisis, high interest rates, a slowdown in construction, a possible general election and two major conflicts in Ukraine and the Middle East unsettling consumers.
In terms of both the home-grown and import sectors, mills are now starting to reduce output to balance supply with demand. We have consolidated production into our larger mills and will, in fact, cut more volume of logs in 2023 than in 2022.
I’d like to say the market’s looking great and 2024 is going to be a bumper year. But I think, with all these factors in play, it’s going to be difficult.
At the same time, at BSW we’re in a balanced position on production and sales. We’ve got a stable, diverse customer base and the acquisition of Scotts last year put us in a good place.
There will also be continued investment in our mills from our parent Binderholz to further improve efficiency and productivity.
We’re additionally seeing a significant rise in sales of Binderholz mass timber construction solutions in the UK and we see prospects for further growth.
We also continue to look at every opportunity to grow use of home-grown fibre and part of the discussion is around its suitability for mass timber. There’s a growing acceptance that in certain circumstances it is suitable and we’ll continue to investigate that going forward.
So, despite the current challenging market, we are optimistic for the future. The UK needs more homes urgently and timber frame has now increasingly got to be a prime solution for building them based on its sustainability, housing energy performance and speed of construction and with the potential of an increasing volume of home-grown timber to be used. But what we need is more than soundbytes from policy makers. A decision must be made at the highest level that, either by directive or incentive, the building industry is going to deliver those 300,000 houses we need each year and that timber frame should be the prime construction method used.