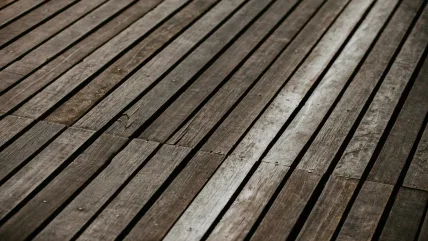
Summary
• Timber frame’s market share is 17.7% according to a Timbertrends report for the UKTFA.
• Total housing starts for 2011 are forecast at 121,500.
• Timber frame is built into budget hotels’ business models.
• Big retailers’ eco stores provide a timber building shop window.
• UKTFA has launched a think tank and training programme to improve supply chain efficiency.
• Kingspan is moving its SIPs production to the UK.
To meet predicted UK housing needs in 2020, starts should be running at a rate of 250,000-270,000 a year. Thanks to the downturn, says the Construction Products Association (CPA), the figure this year is more likely to be around 121,500.
To say the least, construction is still going through torrid times and the UK timber frame sector acknowledges that it hasn’t escaped the pain. What is more, say manufacturers, for the immediate future it looks like more of the same. So, with little prospect of imminent major relief from the wider economy, their fortunes will be dependent largely on their own resources, initiative and ability to win market share.
“The CPA predicts a 7% increase in completions in 2011, but a further 4% contraction in 2012,” said UK Timber Frame Association chief executive Andrew Carpenter. “The private sector is failing to offset the downturn in social housing construction, where timber frame has been particularly strong, and next year we’re likely to see government and local authority spending cuts affecting the wider economy more. The government says it is focusing on construction. There’s talk of relaxing planning rules and releasing more public land for building and David Cameron spoke at the Tory conference about measures leading to construction of 150,000-200,000 affordable homes. But these things now have to happen.”
Geoff Arnold, managing director of timber frame manufacturer Pinewood Structures, agreed. “After a reasonable start to 2011, social housing died a death,” he said. “There’s been a big change in funding models for social rent schemes, resulting in major contraction. The target for a development used to be 40% social housing. Now we’re looking at a quasi-private model, with schemes having to sell as much of the development privately as possible.”
Public spending cuts
“Cuts in public spending continue to impact the market,” said Stewart Milne Timber Systems (SMTS) sales and marketing director Gary Yeoman. “Several projects have delayed start dates, impacting on the wider supply chain.”
“Social housing tends to be seasonal, with business tailing off in the second half,” said Kingspan Potton commercial and sales director Tony Hutchison. “But funding issues are increasingly entering the equation and exacerbating this slowdown. Our view is that we’re not going to see much market improvement through 2012.”
Private housing building, say manufacturers, has also become more jittery.
“It started 2011 better, but wider economic worries and the eurozone situation have created uncertainty,” said Mr Arnold. “Mortgage availability is still relatively poor and the big builders have restructured to make money operating at a lower level, which means fewer houses built.”
Market share
The consensus is that timber frame has defended housing market share this year at around 18%. But it hasn’t been easy, with suppliers across rival construction materials sectors “cutting prices and margins to unsustainable levels and below”.
There is also a debate as to whether its fast build capabilities, which benefited timber frame in better times, now count in its favour.
Mr Yeoman says they do. “Private developers continue to convert to timber frame to reduce build programmes and ensure quicker return on investment, “ he said. “The same applies to the affordable sector, with contractors looking to reduce prelim costs and improve cash flow.”
Mr Arnold gave a different perspective. “We’re seeing some developers build show homes and a first tranche of properties on a site in timber frame, then do the rest in masonry. Build time isn’t such an issue and some contractors think masonry gives better continuity of trades.”
Bright spots
But within the context of a tough overall market, there are brighter spots for timber frame. Education demand is still reported to be “quite strong” and hospitality is “remarkably resilient”.
“Timber frame is at the heart of the budget hotel industry business model, and their investor statements about projected room increases suggest growth will continue,” said Mr Arnold.
The supermarket chains’ increasingly high profile “environmental statement” stores are also a plus. “Tesco and others are committing to building more eco stores and putting timber front of house to be seen to be green,” said Mr Arnold. “There may be an element of PR here, but it gives us tremendous exposure.”
Self-build has also brought some relief, said Kingspan Potton, an important player in the sector. “It’s off a low base, but we have seen improvement in self-build in 2011,” said Mr Hutchison. “Housing minister Grant Shapps has recognised it as a key element in construction and committed to make it easier for self-builders to get plots, finance and planning permission. The market has felt more confident.”
Timber prices
Timber price stability has helped too.
“We work to fixed price contracts, so when raw material prices were rising month by month, it hurt,” said Mr Arnold. “The current situation is a definite improvement.”
At the same time, the timber frame industry says it has become increasingly proactive, on a collective and individual business level, to boost competitiveness and defend margins in the current climate.
The UKTFA recently announced the launch of its Academy education initiative to improve supply chain efficiency.
“I came to the UKTFA from Constructing Excellence, which was set up in the wake of the Eden Report and focused on lean manufacturing, and I’m hoping to share that experience with timber frame,” said Mr Carpenter. “The Academy programme, which leads to an NVQ-level qualification, will show companies how to cut waste of time, effort and materials through supply chain efficiency. And we’re already getting suppliers from the timber and windows sectors to participate too. “
Supply chain
The supply chain focus has to be upstream to the designer and specifier too, he added.
“Timber frame companies still have architects coming to them with projects designed for build systems they’re more familiar with, which have to be redesigned and re-engineered for timber,” he said. “Closer links with the architectural and specifier sector should cut this duplicated time and cost.”
As part of its supply chain push, the UKTFA is liaising more closely with other trade bodies and hosting quarterly think tank meetings involving architects, and clients, including Sainsbury, Whitbread and Crest Nicholson, to improve the “two-way communication process”. It has also established a self-build group and is building on its fire safety work. Following the introduction of its Site Safe contractors’ code of conduct, it has been working with the Health & Safety Executive and Fire Protection Association on “fire growth testing”. The resulting guidance on separation distances for timber frame will form part of a suite of new UKTFA material unveiled at its “Fire Summit” at the London offices of architects’ body RIBA on November 10.
Product development
At the same time, manufacturers are looking to add value and boost competitiveness through product development.
Pinewood is focusing on aspects such as scaffoldless erection and delivering more prefabricated components to site; panels incorporating windows and other fixtures, for instance.
“We’re not convinced the complete closed panel, with plasterboard in place, delivers much benefit, but we’re looking at other areas to enhance the product and capture more value through innovation,” said Mr Arnold. “For a recent Thames Gateway 64-house project we managed airtightness and delivered panels complete with windows.”
As the market moves to higher levels of the Code for Sustainable Homes (CSH), he added, there will be even more opportunity for value-adding prefabrication and product enhancement.
Gary Yeoman agreed, pointing to the take-up of STMS’s Code level 4 Sigma II build system, which has just achieved BBA accreditation, as evidence. “It’s been used by a number of clients, including Scottish & Southern Energy,” he said. “We’ve also completed the Homes & Communities Agency Design for Manufacture site in Aylesbury using it, building 94 houses in 16 weeks.”
Both Pinewood and Kingspan Potton said they are also looking at incorporating more engineered timber. In fact the latter is already using LVL and glulam, with the aim of eradicating all steel elements from its homes.
Tough 2012
While 2012 will be tough – one manufacturer wanted to fast forward to summer 2013 – timber frame companies and the UKTFA believe such product enhancements, especially those that boost environmental performance, will help them through the downturn and give them strong prospects beyond that.
On another positive note, Joe Martoccia, managing director of timber frame oriented consultancy Avebury Projects, also said there are now signs of some government funding being retargeted at social housing, “unblocking schemes which have been on hold”.
Looking ahead, he agreed, timber frame would also gain share as higher levels of the CSH and Building Regulations Part L are implemented. “There’s a time-lag between new codes and new thinking in building, but there’s evidence that this is now [happening], with more schemes coming across our desks where timber frame is preferred,” he said.
Another company expressing its confidence in the future is Kingspan Potton. It is seeing rising demand for its houses built with structural insulated panels (SIPs) from sister company KinsgpanTEK – in fact, they’re now being used in its £3m contract for Barratt’s new zero carbon development, Hanham Hall. Consequently Kingspan Group is transferring SIPs production from Germany to its Selby insulation plant. Annual capacity will be 120-150,000m².