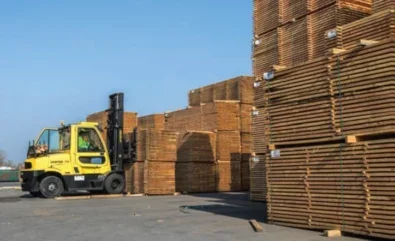
Operations in the wood industry such as sawmills and timber yards have long relied on internal combustion engine (ICE) power for their forklift fleets to keep product moving. But as electric options advance and expand, delivering performance comparable to dieselpowered material handling equipment, timber operations have new questions to ask about clean power and its ability to deliver the productivity that they need.
1. WHICH APPLICATIONS AT TIMBER MILLS HAVE THE GREATEST POTENTIAL FOR FORKLIFT ELECTRIFICATION?
Shipping and receiving – that’s where the greatest opportunity is currently. These mill applications typically have their forklifts, often with lift capacities of around seven tonnes, operating for about a shift and a half per day, or 1,500 to 1,800 hours annually. Because these trucks are running for only 12 hours per day, the battery for electric trucks can be charged while the truck is already out of use anyway, enabling a shift to electric equipment without impacting productivity.
For production workflows, the shift from diesel to electric forklifts is generally on the more distant horizon. That’s because the production departments at mills typically require forklifts to run more continuously than shipping and receiving operations. In production, it’s not uncommon for heavyduty forklifts with a 16-tonne lift capacity to be used to push 200+ tonnes of timber into kilns. While electric trucks are available in this capacity range, the duty cycles for these mill applications are not always compatible with the charging cadence required to keep the trucks powered. Forklifts pushing timber into kilns are often running 4,000-plus hours per year. Operators typically all take their break at the same time, and it can be a challenging cultural change to move operators to staggered breaks. So, mills considering electric for these workflows may need one charger per truck so that operators could have the opportunity charge their batteries simultaneously during the break.
At this point, the business case usually does not favour the cost of both charger and electric truck relative to an ICE alternative, though that calculation is evolving. Advanced electric-powered equipment is expected to become more cost-competitive over time, and some grants can help bring the cost closer to that of a comparable ICE model. Local organisations and government offer various grants, funding, tax incentives or carbon offset credits.
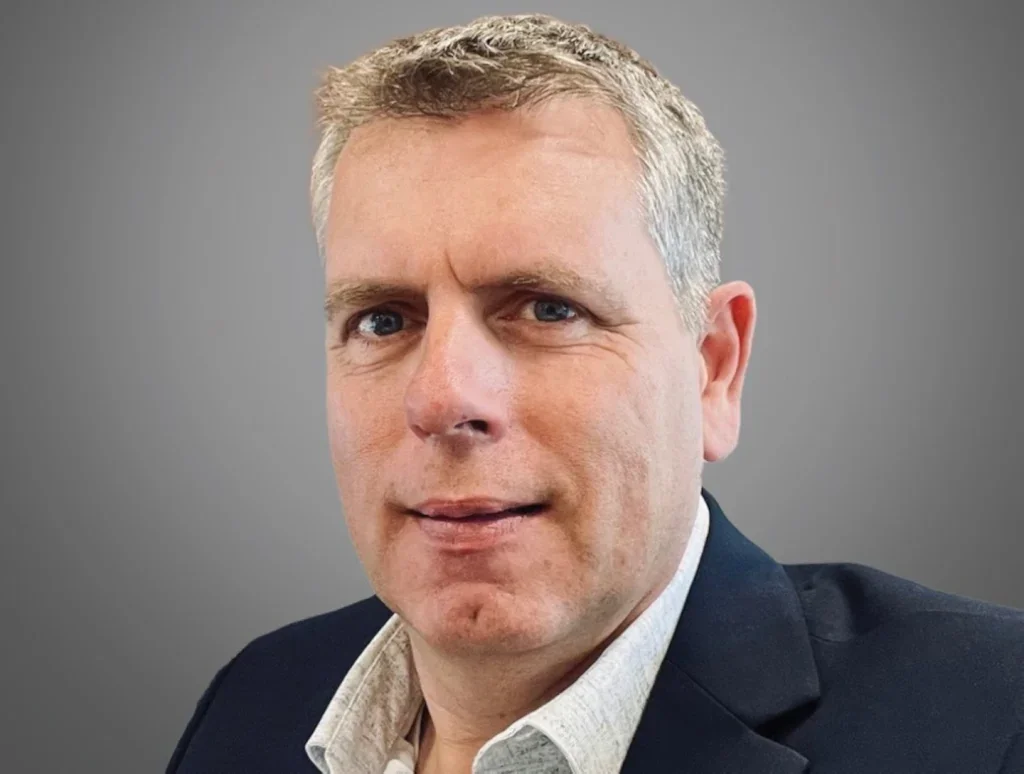
2. WHAT CAN WE EXPECT OUT OF ELECTRIC-POWERED TRUCKS?
Physically, they are the same rugged, dependable forklifts that mills have long known and trusted. Take as an example the Hyster electric and diesel models in the seven to nine tonne capacity range. With the electric truck, the engine and transmission of the diesel model are replaced by two motors, one for drive and one for hydraulics. These efficient, high-power electric motors, paired with the high-voltage lithium-ion batteries, deliver performance comparable to an ICE and batteries maintain consistent power delivery throughout the full battery charge.
3. WHAT ELSE SHOULD WE KNOW ABOUT THE BATTERY?
If your mill is considering an electric forklift, ask about the type of battery that will be used to power the truck. Some manufacturers’ high-capacity electric forklifts are powered by lead acid. While lead acid is a well-established power source and a strong fit for some applications, in trucks of these capacities, the lead acid battery would be so large and so heavy that it can require another forklift just to remove it for cleaning, watering, cool down, and charging. Because of the time required for battery maintenance and charging, multi-shift operations using lead acid typically need more than one battery per truck, and in turn, battery maintenance, and storage space.
Lithium-ion batteries, on the other hand, are smaller and lighter, and do not demand the same intense battery maintenance and cooling requirements of lead acid, which can enable the operation to purchase and maintain fewer batteries per truck, alleviating the high cost associated with dedicated storage space for batteries. If the battery is lithium-ion, confirm whether it is integrated by the factory or requires an additional purchase and installation. Some electric forklifts have a strategic design that incorporates the lithium-ion battery, creating more space in the operator compartment for maximum comfort.
4. WHAT ARE THE CLEAREST BENEFITS?
For one, electric forklift options can help businesses reach emission reduction goals, whether those are self-imposed or required through government regulations. One major advantage of an advanced electric power option like lithium-ion batteries is that they produce zero tailpipe emissions while in operation or charging.
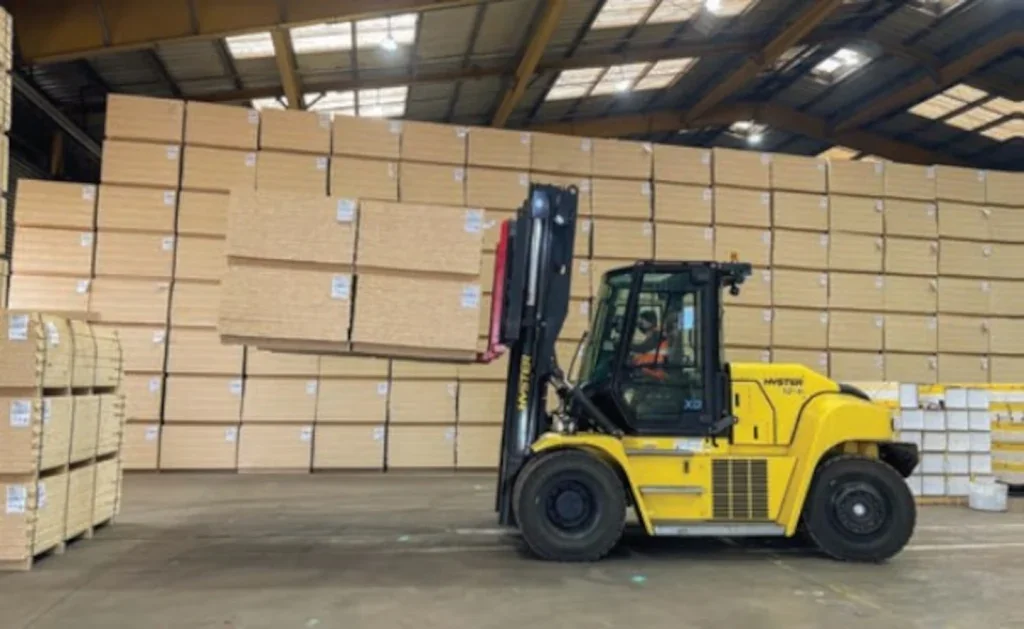
But electrification brings more to the table, particularly when it comes to the maintenance and longevity of equipment. While all forklifts require maintenance, the maintenance requirements associated with particular power sources vary. Electric drivetrains have fewer components and less complexity than ICE, and therefore fewer serviceable parts that require periodic maintenance. Aside from maintenance, the power source can have a major effect on the useful life of equipment. An average, moderately used ICE truck has an economic life for the first owner of about 10,000-12,000 hours, whereas similarly maintained lithiumion trucks could surpass this mark, potentially reaching 20,000 hours.
However, battery electric is not the only mechanism operations are exploring to enable a shift to clean power. In some cases, industrial trucks are being powered by hydrotreated vegetable oil (HVO) 100, a bio-based, renewable liquid fuel diesel alternative that can eliminate up to 90% of net greenhouse gas emissions, such as carbon dioxide. Some industries are also leveraging hydrogen fuel cells (HFCs) to power heavy-duty equipment like container handlers. Hydrogen fuel cells produce zero harmful emissions in operation and refuelling, emitting only water and heat as by-products.
5. WHAT CONSIDERATIONS DOES THE TIMBER INDUSTRY NEED TO ADDRESS?
Grid stability remains an important factor that mills must consider when evaluating a shift to electric equipment. Most mills run about six to eight high-capacity forklifts. The amount of power required for charging eight electric trucks is significant – about a megawatt of power. To put that in perspective, the average European household uses under 10 kilowatts per day. That means the megawatt of power required each day to charge this fleet of trucks would power an entire house for several months.
Globally, mills are in very remote locations, where grid stability can be a challenge with an energy draw of this magnitude – and material handling applications are not the only ones with growing demand for utility infrastructure and reliability. The UK government supports the transition to electric on-road vehicles as a means to reduce carbon emissions. While the National Grid confirms that it can cope with the increased demand from electric cars, it is unclear whether the transition towards battery electric industrial trucks or larger vehicles has been accounted for in these calculations.
Green energy is another area currently in development. While a growing portfolio of electric forklifts produce zero tailpipe emissions, not all electric power is from green or renewable sources. Fossil fuels still generate 33% of the UK’s energy, though in 2023, low-carbon sources made up 56% of the UK’s energy sources, of which renewables were 43%. Wind generation outstripped gas sources for the first time in 2023, with clean generation reaching more than two-thirds of EU electricity in 2023, double fossil’s share. While the electricity generated in the UK in 2023 had the lowest-ever carbon intensity, there is still a journey to reach the government’s goal of 95% low-carbon electricity by 2030, and full decarbonisation by 2035.
MAKING THE POWER SOURCE DECISION
The shift to electric forklifts in the timber industry offers significant opportunities, where electric trucks can meet productivity demands. As electric technology evolves, the potential for broader adoption grows, but key considerations, such as grid stability and energy sourcing, will play crucial roles in determining the feasibility of widespread electrification. While electric forklifts can significantly reduce emissions, ensuring green energy sources and reliable infrastructure are essential to fully realise the benefits of clean power in material handling.
As businesses consider how best to electrify, consulting with an expert can help weigh up the strengths of each option and determine whether lithium-ion batteries are the right long-term fit.