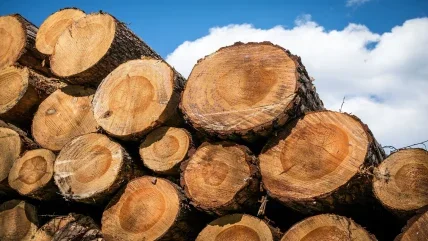
Current economic conditions and consumer caution may pose challenges for suppliers, but all the indicators point to a buoyant future for timber cladding in the UK, according to latest analysts’ reports.
In its review of the sector, Mordor Intelligence (www.mordorintelligence.com) predicts a compound annual growth rate of 4% for the next five years. Factors driving “significant” market expansion, it says, will include “lower interest rates, increasing real disposable incomes and numerous [public building] investments by government”.
If anything, the perspective of the justpublished UK Timber Cladding Market Analysis from Markwide Research (www. markwideresearch.com) is more positive still. It says the business “offers significant opportunities in coming years”.
Its upbeat forecast is partly down to recent new product development and resulting performance improvements, which are helping counter consumer perceptions that timber cladding is high maintenance.
“Advances in wood treatment and development of modified wood [mean the sector can] offer products with enhanced durability, stability and resistance to rot and pests,” states Markwide.
Timber cladding’s environmental credentials will also increasingly add to its momentum, it maintains, given increased architect and builder focus on sustainability, rising consumer climate change concern and regulatory moves to decarbonise construction.
Building regulations, says Markwide will continue to drive sustainable construction practice, including use of “eco-friendly materials”. In a related development, it also sees the market benefiting from growing adherence to green building codes, such as BREEAM – uptake of which grew 13.9% from 2019-2020.
“Builders and developers seeking green building certifications may prioritise timber cladding as the sustainable, eco-friendly choice,” says Markwide.
At the same time, it predicts a further rise in the popularity of biophilic design among specifiers and consumers, with its emphasis on bio-based, and health enhancing materials in construction. “Timber cladding aligns with this trend, allowing seamless integration of a natural material in buildings [which is seen as] enhancing the overall well-being of occupants,” says Markwide. “Its natural insulating properties can also contribute to energy efficient design, helping government and industry meet sustainability goals.”
Adoption of latest technologies, such as 3D and building information modelling and digital fabrication, is also set increasingly to drive the sector. “They can streamline cladding design and manufacturing processes, resulting in cost savings, greater precision and faster production,” says Markwide.
Given wood’s relative strength to weight and simplicity of processing, it says, timber cladding is also set to increasingly become an exterior finish of choice in the rapidly growing, government-supported offsite housing manufacturing industry.
Many of Markwide’s comments are echoed by cladding and cladding materials suppliers. They acknowledge that the cost-of-living crisis more recently has dented market confidence. But they share Markwide’s confidence in the medium to longer term of the business. And this is reflected in continuing product innovation and market development.
Due to challenging economic conditions, Accsys Technologies has seen some recent “softening of demand” for its Accoya modified timber.
“But the UK has been relatively resilient and we’ve just reported a 20% increase in Accoya volumes sold over last year worldwide, of which cladding is our second biggest end use,” said Accsys head of marketing Laura Keily. “In the UK, windows and doors is our primary market and we see huge potential to build on this and develop our cladding proposition. We’ve invested in a dedicated specification manager to focus on this.”
Accsys also continues to see good momentum for Accoya in the commercial sector, with brands, including M&S and B&M, wanting to visually demonstrate their sustainability credentials in their buildings, using more biophilic design and natural materials.
Timbmet commercial director Paul Holstead agreed that the wider economic slowdown had affected the sector. “The pandemic home improvement boom is well and truly over,” he said. “All markets are impacted. There is still demand out there, but you have to work harder and smarter to secure it.”
Timbmet had also seen the market “moving away from the norm”.
“Larch supply has dried up for obvious reasons. And, while it’s reduced a little, cedar has seen record high prices in 2023,” he said. “But our customers have been open to looking at alternatives. We developed a volume of Red Grandis into the cladding market in 2023 and we also launched the ultra low thermal value Abodo range in Q4. It has seen unprecedented opening demand and acceptance by the market and we see further volume growth in 2024.”
David Johnson, general manager at James Latham’s producer Dresser Mouldings said the company had also seen cladding sales coming down from their peaks of the pandemic home improvement surge.
“From the feedback we’ve had from residential clients, with less disposable income around and the façade usually being one of the last parts of a project to be completed, it can be impacted,” he said.
But he added, Dresser continues to serve a broad cladding market, ranging from self-build to its main customer sector, commercial building. It has also seen market diversification. “With the reduction in availability of larch, we’ve seen an upturn in other species such as Douglas fir and thermally modified timbers, with Accoya cladding sales, particularly coated Accoya, continuing to grow.”
New to the Dresser product offer for 2024 is ‘coloured-to-the-core’ Accoya Color, which Accsys has just made available in the UK.
“Accoya Color has had a great reception in the US, DACH (German, Austrian and Swiss) and French markets,” said Ms Keily. “It has strong traction in decking, given its durability, protection from scuff marks and low maintenance. For the same reasons, we’re now seeing good momentum in cladding. It’s an attractive weathered grey colour – so no need to wait for natural weathering – and it’s low maintenance. Our UK customers have been asking us about it for some time so we’re pleased we can now offer it.”
Abodo is also a modified timber, which, says Mr Holstead, has a range of attractions for the market.
“We’re delighted to have signed our distribution agreement with Abodo Wood, one of the world’s leading modified timber producers,” he said. “As well as having ultra low thermal values, and offering Class 1 durability, it’s the UK’s first carbon negative feature timber. It’s FSC-certified and has a 15-year warranty against fungal decay and delamination. It also machines and coats with ease and it’s backed by a market-leading promotional and brand package.”
Other trends noted at Dresser include specification of unfinished Accoya in rainscreen and feather edge sections, while demand for shou sugi ban charred finish products increased at the end of 2023.
Sales of Dresser’s fully finished Accoya Finish Line range have grown too, especially in shadow gap cladding, with greys and blacks popular colours.
Another important move has been development of an Environmental Product Declaration (EPD) for Accoya cladding through Bangor University “as part of James Latham’s carbon footprint story”. The company has also focused on marketing to merchants to drive sales of cladding and Sansin coatings, for which it is sole UK supplier.
Timbmet also upped its cladding communication and marketing in 2023. “We want to raise awareness of the Timbmet offer, and there’s still some work to do on this in 2024,” said Mr Holstead. “Watch this space.”
Looking ahead, Timbmet also sees strong prospects for its sales of Composite Prime cladding. “They increased significantly in 2023, due, we believe, to the increased cost of cedar, reducing larch supply and the natural evolution of the composite market,” said Mr Holstead. “We don’t see this growth slowing.”
A continuing challenge for the timber cladding sector, said Ms Keily, is arguing its fire safety case following the introduction of new building regulations on use of combustible materials in walls.
“This is certainly the case in the commercial market, where [specification] decisions are often driven by insurance companies, who are very risk averse in this regard,” she said. “As always with fire, it’s important to test and ensure compatibility of auxiliary products. The challenge is the discussions that don’t reach us because timber cladding has already been ruled out early in the design stage – even though it would be permissible under building regulations. But we are successfully getting the message across that Accoya can be treated to meet higher requirements.”
Overall, she added, Accsys too is taking an upbeat outlook. The additional Accoya production capacity that came on stream last year, it says, has been welcomed by the market, and construction of its joint venture Accoya plant with Eastman in the US is on track. Its TV advertising last year, it maintains, has also increased brand awareness.
“We expect some of the softer market conditions to continue through the first half and then demand to pick up again,” said Ms Keily. “Long term the prospects for Accoya cladding are very strong as we need more housing and we need to build it sustainably.”
Dresser also sees cladding markets increasing, as “more designers and consumers choose sustainable materials”.
“There has definitely been an upturn in timber as a material of choice in construction due to its availability, versatility and low carbon footprint,” said Mr Johnson. “Architects and designers appear to have the desire for and see the marketability of sustainable, ethically sourced products [as part of] carbon efficient projects.”