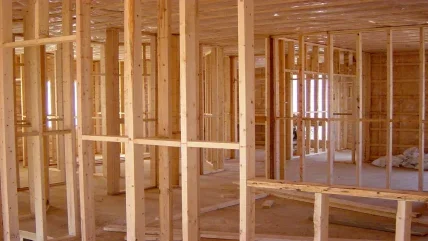
Running safe operations is a priority in all stages of the wood industry life cycle. However, when any job or activity becomes second nature, familiarity may breed inattentiveness – a sense of “autopilot” kicks in and carelessness can result. Or, if a task or job can be completed more efficiently using some sort of shortcut, human nature will often dictate that action. Unfortunately, both distraction and corner-cutting can lead to disaster for the individual and others.
In materials handling operations, such as wood production or storage facilities using forklifts and industrial trucks, safe practices involve multiple layers of application, from truck and machinery operations to employee and visitor conduct. And, although every environment has unique challenges, consistent safety standards should be woven into every facet of business. Many associations have established specific weeks or days to raise awareness of safe practices when it comes to materials handling. But safety cannot be confined to a particular day or month.
For many organisations in the timber industry, a shift may be needed towards a culture where safety is everyone’s job and should extend across operations and the supply chain.
When assessing the various levels of risk mitigation and elimination, comprehensive occupational safety involves a “hierarchy of controls”, which includes engineering, administrative controls, and personal protective equipment (PPE).
ENGINEERING
The foundation of safety is established with years of engineering work and lab testing. In fact, Hyster has a long association with the wood industry having originally been a logging equipment manufacturer in the 1920s. So, whether it’s for a facility or an industrial truck, the Hyster engineering experts understand that risk reduction must be inherently designed in.
When forklift operations are assessed, people typically look at efficiency, handling capacity and so on. However, engineering has developed a vastly different forklift over the past 50 years. It’s not only more efficient but also more comfortable and markedly safer. Many of these engineered safety features are taken for granted, for example, overhead guards and seat belts. Once not understood as necessary at all, overhead guards today are designed with strength and rigidity to protect operators from falling objects, while allowing for crucial visibility.
In today’s wood industry, operators are extremely influential in the decision making process and safety and driver ergonomics are key. Advances in ergonomics have positively impacted operator safety. Operator Assistance Systems (OAS) and engineered comfort allow for operators to sit in a truck for six, seven, or 10 hours without the pain or injury issues of the past. Ergonomically designed lumbar support, padding, reachable controls, and visibility have helped improve operator safety.
Improving awareness of forklift truck drivers, and pedestrians working nearby, may also help reduce incidents. While Hyster trucks are designed as standard with operator awareness and visibility in mind, now businesses can further customise their fleet with application-specific solutions.
For example, the Dynamic Pedestrian Awareness Light from Hyster can be mounted to the front or rear of a counterbalance lift truck. The compact blue LEDs project a progressively flashing blue arrow pattern in a straight line on the floor. This eye-catching light gives a visible indication that a truck is approaching, where it is approaching from, and the truck’s direction of travel, helping signal the position of the forklift to pedestrians or other vehicles. This can support safety in certain applications that may have blind corners, cross aisles, high foot traffic, or unloading operations where visibility of working lift trucks is restricted.
The patent-pending Reverse Speed System is also available for selected Hyster lift trucks. It places a sensor next to the rear drive handle on the lift truck, which can detect if there is a hand placed on the handle. If there is, it will allow the lift truck to reach full reverse speed. If the sensor is not activated, the reverse speed is limited to 2km/hr. Holding the handle encourages the operator to look in the direction of travel while reversing, as is standard practice. Wood operations using high numbers of temporary or agency staff may find it particularly helpful for upholding their operating standards.
ADMINISTRATIVE CONTROLS
Administrative controls are location-specific and multi-faceted – and they are typically a result of local health and safety authority and government mandates. These regulations, though, are merely the minimal expectation of standards. However, the people who create the standards aren’t on the job day in and day out. Rather, they go on-site only when there is a significant incident.
For administrative controls, such as policies, procedures and training materials to be effective, they should reflect an understanding of an organisation’s own climate. It is important to consider what is done specifically on the wood handling site, which types of trucks are in use, and how they are being used. Certainly, policies and training must follow regulations, but they must also go above and beyond to be sitespecific, truck-specific, and operator-specific.
Timber businesses should also seek out training resources developed by experts in the materials handling field, including manufacturers, dealers, and those who operate these trucks daily. Training is never a oneand- done activity; instead, it is a recurring cycle of training, evaluation, and follow-up. Moreover, when dangerous actions and/or behaviours are witnessed, operation leaders must take swift action and give immediate consequences, including hands-on mentoring, retraining, or probation.
Telematics systems may also play a helpful role here. Hyster Tracker wireless asset management, for example, can aid in providing best practice operations. Card reader access to equipment will help limit access only to those card holders that are licensed and authorised. Meanwhile, automated pre-shift checklists can help you achieve peak operator compliance. The truck will not operate until the operator has completed a standard pre-shift checklist or a specific industry mandated checklist.
Hyster Tracker proactive monitoring systems will send notifications in real time to address events in an effective manner, with instant follow up. For instance, impact detection can help improve site safety measures and aid in reducing avoidable damage through accurate impact monitoring and real time alerts. In critical impact events, the system also enables assets to be shut down to ensure the equipment is inspected before returning to operation. Managers can also measure utilisation by operator to better understand who is causing avoidable damage at the site.
PERSONAL PROTECTIVE EQUIPMENT
In the hierarchy of controls, the last line of defence is PPE. Wearing hard hats, gloves, and protective eyewear and using on-board safety features fall under this category. This safety aspect also includes proper care and maintenance of PPE. All these components have been engineered for safety and perhaps mandated by administration, but the action to implement them is primarily at operator or individual level.
PEDESTRIAN SAFETY
Pedestrian safety is a vital aspect of overall forklift safety in wood handling applications. Everyone working around trucks – employees, vendors, and visitors – must be trained to understand their risks and responsibilities.
In addition to a safe facility layout, including the clear marking of pedestrianonly aisles, shared aisles and so on, Hyster encourages a pedestrian safety best practice called “Wait for the Wave.” It’s a deliberate action between operator and pedestrian to acknowledge, “I see you and I value your safety. I will wait and wave you on.”
CHOOSING SAFETY
Regardless of the level of control, safety is ultimately an individual choice. Every person, every day, should make the correct decision every time. In fact, choice encircles the entire occupational safety environment and has been the primary focus of safety professionals and management for the past decade.
For example, even though a flywheel guard has been engineered for operator safety, that operator must make the decision to keep that guard in place and inspect it regularly. And, although a facility’s pedestrian training programme could be ideal, a visitor may choose not to follow that rule. Moreover, every operator has a personal choice to don a hard hat or eye protection; some will make the correct choice, but others will not. The decision comes down to the personal value one places on their safety – and the safety of those around them.
Globally, there are yearly fatalities directly and indirectly related to forklifts. There are also numerous injuries related to forklift operations, which may be severe enough for the impacted persons to lose time at work. Although these numbers have reduced significantly over time, they are still unacceptable. For forklift operations, zero injuries should be the goal. Every single operator should leave work the same way he or she came in.
The bottom-line goal for occupational safety professionals covering materials handling operations (and beyond) may be to develop a true culture of safety recognition and action, where environmental health and safety professionals are needed less and less.