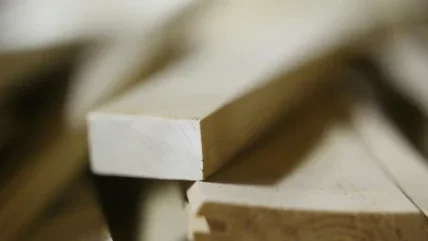
The chipboard market has entered the summer in a reasonable state of balance, with most product segments experiencing decent, if unspectacular, levels of demand. But despite relentless cost pressures, domestic producers are agreed that this is not the moment to be approaching the market for further price increases.
Raw board products increased by an average of 5% at the start of the second quarter, and this became relatively well established in the market despite evidence of slightly more competition from the Continent.
But with the onset of the traditionally “unexciting” summer period, it was unlikely that the next price hike would be sought any time before September, one producer said.
According to another UK producer, his company would be looking to renew price negotiations in the late summer with a view to implementing the next increase for around September. While he wouldn’t quantify the exact scale of the next increase at this stage, he said that a rise of 5% was “a sensible expectation”.
For its range of MFC products, a prominent overseas supplier into the UK market confirmed that it was looking to establish a price increase of around 5% before the main summer holiday period in order to help offset the cost increases incurred during the past 12 months.
According to a senior domestic producer figure, cost pressures were continuing to be applied by “the usual culprits”: his facility’s methanol bill had jumped 15% between the first and second quarters of this year; melamine costs had soared 57% year on year and were “showing no signs of going down”; and wood prices had also risen, although perhaps not to the same extent as in western Europe. And even though energy prices had fallen going into the summer, they were still higher than at the same time last year, a fellow producer added.
Raw material costs Another contact said: “The increase in costs of raw materials has been partially transferred to the prices for MDF but not for chipboard, and the gap between these products is getting bigger.”
Domestic chipboard producers appear to be entering the summer holiday season on a reasonably positive footing. Capacity utilisation is high and production is widely expected to continue – except for planned maintenance breaks – throughout the summer. Indeed, one domestic producer said that stocks had dropped to quite low levels for the time of year and that the seasonal decline in demand over the summer would provide an opportunity to rebuild inventory ahead of the busier autumn period. Producers also told TTJ this week that demand had improved in the second quarter following a weather-hit opening three months to the year, to the extent that chipboard sales volumes had been “better than expected” and higher than those achieved in the same period last year.
The T&G market had “picked up”, solid MFC sales pointed to better order books for most furniture manufacturers, and interest from retail customers had also improved. Another chipboard producer agreed that the furniture sector was showing some – but “not huge” – strength, while the worktops market was better than at this stage in 2012.
Sales of chipboard into the UK building sector have been more mixed, with certain parts of the country – notably south-east England – performing significantly better than others. But overall, producers were pointing this week to evidence of “a bit more consumer confidence” leading to increased purchasing activity on higher-value items such as cars and furniture.
Impact of Knowsley closure As anticipated, the closure of Sonae’s facility at Knowsley last September has benefited other players in the UK market, most notably in the T&G and MFC segments – the latter of which was described this week as “the leader” of the chipboard products. But even in this reasonably strong MFC market, some contacts identified “plenty of competition at low prices, especially in commodity items like white”.
The plant and equipment used at Knowsley have now been earmarked for various Kronospan companies in eastern Europe. But in this context it should be recognised that Sonae has retained some large accounts in the UK and has thus continued to send chipboard here from group mills on the Continent. This flow goes some way towards explaining a steep increase in UK chipboard imports over recent months, with the latest Timber Trade Federation (TTF) statistics showing a 24% upturn from 108,000m³ in the first quarter of 2012 to 134,000m³ in the corresponding period of this year. The TTF has noted that the biggest increase in imports was from Portugal, followed in order by France, Spain and Belgium. However, the UK market continues to be a largely unappealing prospect for overseas suppliers. “We aren’t bringing any standard chipboard into the UK market because of logistics costs and prices,” said a UK-based spokesperson for a Continental chipboard producer. He added that the prices paid by major users in this market were at a “very low” level “which I doubt gives any return to the manufacturer”.
According to other contacts, raw board prices in the UK are lower than those prevailing widely on the Continent, thus combining with currency and transport cost considerations to restrict the flows crossing the Channel, despite generally weaker demand on mainland Europe.
UK export figures down As for UK exports of chipboard, the latest TTF figures indicate a 67.8% slump in volumes to 19,000m³ in the first quarter of 2013 from 58,000m³ in the corresponding period last year; indeed, the total for the first three months of this year was well below the 28,000m³ recorded in February 2012 alone.
In its review of the first quarter, Sonae confirmed that the plant closures at Knowsley and at Solsona in Spain last year were “part of a continuing strategy to adapt our industrial footprint with the aim of reducing fixed costs, improving operating efficiencies and increasing capacity utilisation in our more efficient plants”. This year’s first quarter was characterised by “a material fall-off in volumes sold” as a result of these closures, seasonality issues and the difficult economic environment impacting the furniture industry.
Despite continuing macro-economic uncertainty, Europe’s panel markets remain “steady”, it was reported by Norbord in its own results package for the first quarter. In this year’s January-March period, average panel prices increased 5% quarter over quarter, with chipboard markets said to be strong. However, Norbord’s panel shipments in Europe were 3% behind those of last year’s first quarter “due to lower retail furniture sales over the holiday period”.
Another major company to have offered a market perspective of late is Egger, with the Germany-based group expressing cautious optimism for 2013/14 on the back of stable market developments in German-speaking countries and eastern Europe plus a slight increase in business in the UK. As previously reported, a £20m resin plant development is taking place at the Egger plant in Hexham and is scheduled for completion next year. And at the same facility, a further £4m has been invested in a new engineering complex. Phase one of the project – including workshops – has been completed within the last few weeks, while new offices and training facilities for apprentices are in line to be finished by September this year, according to a spokesperson.
The same contact also confirmed that the fire at the Hexham operation’s biomass boiler facility over the late-May Bank holiday had led to the loss of around 36 hours of chipboard production while the lamination line was down for some 24 hours . The incident had had “very little impact” on the business’ overall stock situation and created no service issues; however, news of the incident had triggered a flurry of buying for stock, TTJ was told.