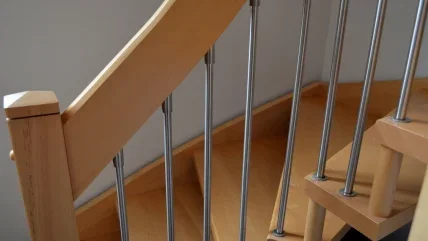
Summary
• Weak demand is compounded by lack of finance.
• Stairs suppliers to volume housebuilders are suffering.
• Last year 18 BWF member companies closed.
• Ecobuild is thought to have boosted orders slightly.
• TRADA says the government’s unclear definition of zero carbon is an impediment to the joinery industry.
The business outlook for the UK joinery market remains one of prevailing uncertainty, with the lacklustre economy driving fierce competition for the business that is available.
Despite the generally gloomy market there is an underlying optimism among manufacturers who expect the market will turn, although some firms say the challenge will be holding out until better times arrive. At the same time there are various pockets of activity keeping, particularly niche, operators busy and there are signs for many that the worst of 2009 is now behind them.
The absence of any definitive joinery market statistics means no-one is able to quantify the extent of the downturn to date and speculation varies as to how hard the industry has been hit. A British Woodworking Federation (BWF) spokesperson said it would take longer for the full impact of the downturn in economic activity to trickle down the construction industry supply chain to hit joinery, compared with other product markets such as concrete or bricks. Regardless of the uncertainty surrounding the levels of activity, indicators point to a continuing downward trend for the foreseeable future.
Lower demand
The feedback arriving at the BWF by the end of March was that there was significantly less work available than a year ago and consequently people had to battle harder to secure business. “Construction of private sector housing has almost ceased. Public sector housing is continuing, but it only makes up a small part of the newbuild market so it is not able to pick up the slack,” a BWF spokesperson said. A mass production joiner said a positive turn was that the self-build sector was resisting the market trend and “people are still buying up land fairly strongly, which is good news relative to what is happening with private newbuild”.
A major casualty continues to be the stairs sector, which has been suffering increasingly throughout the past year. The larger joinery companies that are locked into the volume housebuilder sector are reportedly being hit the hardest.
The points related by the BWF were backed up by several firms, with one established window manufacturer saying the problem with decreasing demand was being compounded by the lack of finance available. However, another manufacturer said that while January and February had been slow, business seemed to be picking up in March. “This is probably a combination of the economy and seasonality; the snow earlier this year certainly didn’t help things,” said the contact.
The deteriorating conditions translated into a higher than usual number of BWF members entering administration or going into liquidation. So far this year four joinery firms, out of 500 on the books, have gone out of business, while 18 closed in 2008, compared with 11 in 2007. A spokesperson said 2008 heralded an unprecedented level of loss, although it only represented around 4% of membership while the majority of the members had already paid up fees for 2009.
Job-seekers
The strongest indication of the state of the market, according to the BWF spokesperson, was the number of calls The Federation had received in the past six months from people looking for short-term work following redundancies and layoffs, another unprecedented situation for the federation. The spokesperson said joinery companies had come under intense cost pressures: “Many of those companies that had to let people go were holding out last year for Christmas, waiting to see what happened. A significant number made their first cuts in staff numbers in summer and early autumn; a smaller group had hoped to avoid it and waited until January, but then had to make the cuts.”
Another outcome of recent conditions is a trend among joinery firms of taking on jobs they would ordinarily shun. “We are taking on whatever comes through the door,” an architectural joinery manufacturer said, “and we’ve been estimating like crazy but getting very little fruit. I understand some are taking on jobs and working for cost just to stay afloat. That seems to be the main goal for 2009, just hanging in there, keeping your head above water until things improve.”
Conditions have been kinder to joinery firms in more specialised sectors, with a senior industry figure saying “the more specialised a business is the more likely they are to still be getting work. Clearly some individuals are still prepared to spend money. Consequently, the work is tending toward relatively high value projects”.
Public sector work
Another area of optimism at the moment is among those catering to the public sector, particularly the areas of health and education. Government investment in these areas has increased and is set to continue rising as plans for 2010 are brought forward a year. However, a senior industry figure said competition for this work was strong and only set to intensify.
As joinery firms compete for market share and seek ways to establish competitive advantage, demand is increasing for chain of custody certification, British Fenestration Rating Council (BFRC) window energy ratings and other product testing. More than one window manufacturer said environmental qualities were assuming ever-greater importance in the role of marketing, particularly sustainable accreditations regarding timber sourcing, energy rating certifications, security and fire door accreditations.
TTJ was also told improvements in joinery work quality and product environmental qualities were proving an unexpected byproduct of the economic conditions. Various joinery firms have noted that specifiers are insisting more than ever on high quality work and requiring specifications like BWF CERTIFIRE for fire doors. “In the past, where you may have been able to negotiate around these points, we are finding clients are more insistent that this is provided. In terms of quality, the situation is enabling specifiers to be more demanding and they are forcing people to demonstrate the quality of what they are producing. It seems likely this will increase and the mindset may be ‘if this can be done in the hard times, there is no reason it can’t be done in the future’.”
One mass production joinery said his approach was to be “innovative, aggressive and on the ball”. “We’re focusing more than ever on improving customer services and, on the jobs that are going ahead, identifying what the customer’s needs are and satisfying them. We’re also helping where we can on issues like finance – helping clients secure funding,” he said.
Being a member of programmes like the BWF Timber Window Accreditation Scheme was proving beneficial in differentiating products, a window manufacturer told TTJ.
So far this year the joinery industry has been well-represented at trade shows, and Ecobuild, held in London in February, was credited by some firms for a boost in trade in March. Window manufacturers are continuing to report a swing in market share from PVCu to wood windows, thanks largely to environmentally-friendly qualities. Ecobuild was used as a platform to release research which is expected to help wood windows claw back more of the market share, of which manufacturers generally agree PVCu still controls about 80%.
Life cycle assessment
Life cycle assessment (LCA) research conducted by Davis Langdon, commissioned by the Wood Window Alliance (WWA), was released showing WWA brandmarked windows to be carbon negative. Researchers measured the embodied carbon of a selection of WWA windows with BFRC A and C energy ratings over 30-, 60- and 100-year building service life periods. Despite carbon emissions from transport, production, maintenance and end of life, the overall life cycle of the wood windows measured in the study was carbon negative, provided the timber was from a sustainable forest and end of life issues were taken into account. The wood used in WWA windows, it says, is sourced from forests that sequester more carbon than they produce because the trees used for window production are continually replaced.
BM TRADA Certification told TTJ that as more firms seek to capitalise on the trend in demand for energy conservation, it is seeing a surging demand for its certification services. A spokesperson said they were particularly seeing strong demand for window energy ratings as firms try to increase the attractiveness of their products.
The certification body says it expects the government’s minimum standard for BFRC window energy ratings to move to level C in the A to G scale. “Our feeling is that companies are looking to offer a range of products to meet the varying needs of clients.”
The Code for Sustainable Homes continues to make an impact. The code measures the sustainability of a new home against nine categories of sustainable design, rating the whole home as a complete package using a one to six rating system to show the overall sustainability performance of a new home. BM TRADA’s spokesperson said the code was “driving up the performance standard in window design”.
TRADA has hit out at what it sees as an impediment to the joinery industry in the government’s unclear definition of zero carbon, “a phrase which defies definition because it is unachievable”. A spokesperson for TRADA said it was problematic for anyone manufacturing joinery products when “the government is demanding zero-carbon products, which would need to meet unsatisfactorily defined criteria”. The association is mounting a campaign that advocates the overall goals for reducing energy consumption but takes an achievable approach.?