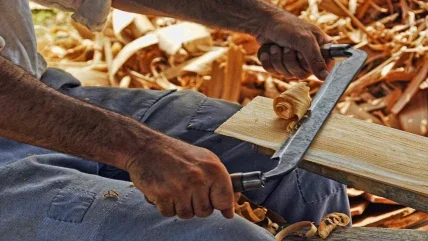
It’s too early to say that the UK joinery sector is on the road to recovery but there is certainly a feeling among some manufacturers that the worst could be over.
The difficult market of the past four years or so was compounded by wet weather over the winter, which prevented some joinery products from getting to site. However, that’s all changed over the past month.
"In the last few weeks it’s almost like the pressure cooker’s been released; we’ve certainly seen a big intake in orders, in fact we had a record intake in May," said one window manufacturer whose main focus is the replacement market.
Although it was too early to say the improvement was a signal of a sustained recovery – "we need to see a few months under our belt first" – his factory was nearly sold out to the end of August and all the signs were that the rest of the year would be good.
"I’m happier now with the state of play than I’ve been for the last three-and-a-half years, but whether it’s a false dawn, I don’t know," he said.
Another window manufacturer was equally positive. "I can see us coming out of this. There’s a spring in people’s steps," he said.
An architectural joiner, which has laid off just over a quarter of its staff since the economic downturn hit in 2008, is having its best period for three or four years.
"We’ve had a bit of a turnaround. The pickup started mid last year; we started to pick up a few reasonable sized jobs which grew by the day as more was added," TTJ was told.
"They’re not large value but they’re the sort of job we need as a mainstay."
The company had also started to recruit again, taking on a couple of people and an apprentice in the last two months, and it was hopeful that the busier workload would continue for the remainder of the year. "But we’re not going silly because, while we’re busy at the moment, we’re cautious," the contact said.
The British Woodworking Federation (BWF) is also sensing a more positive mood.
"It’s starting to look better," said a spokesperson. "We’re starting to hear stories about busy pipelines and busy factories in some parts of the industry."
However, he conceded that activity was still at a low level and the market remained competitive.
And while some manufacturers are busier, it’s from a low base and they point out that the market is still tough, especially for smaller companies and those reliant on the volume housebuilding market.
One manufacturer said the joinery fit-out market was pretty much dominated by larger joinery companies which were securing contracts and subbing them out to smaller firms.
An added pressure for all joinery manufacturers, big and small, is the rising cost of softwood, said to have increased by 20% this year.
"The price has gone up so rapidly that you can’t always put your prices up as quickly as you want to," said one manufacturer.
Contracting pressures
For joinery fit-out, another contact said, the impact of higher raw material costs was exacerbated by contractors dictating the price of a job. "We’re almost being told ‘this is what people want to pay’," he said. "Contracting is very much ‘this is the budget we have, if you can’t do it we’ll find someone who will’."
He added that contractors also expected manufacturers to do more, forcing them into areas they would not have considered. "They no longer want you just to supply; they want you to supply and install but a lot of joinery shops don’t have the resources and insurances in place to install.
"Contractors have you in a vice and you have to play their game," he said. Several contacts said the burden of red tape was also felt more keenly.
"It’s almost too much before you even start to make something," one said.
The BWF agreed that regulation compliance was a big pressure for manufacturers. "This year there is Building Regulations Part L, CE marking and the EU Timber Regulation all subjecting companies to fairly major change over a 12-month period and all require systems to be put in place," the spokesperson said.
"EUTR and CE marking should be light touch for most companies but they still require time to understand how they relate to their businesses, and inherently they do carry a cost."
The BWF was helping members by providing template documents and processes, he added. Although the BWF expects demand to improve over the next six months there will be no step change unless there’s a radical change in government policy.
"There are two things the government can do to improve the market radically, everything else is tinkering around the edges," the spokesperson said.
Those two things are public investment in housing and a cut in VAT on construction work. "If we could get the VAT rate down it would add incentive for people to get work done, and to do energy-related work through things like the Green Deal.
"The European Commission is taking the UK government to court over the differential VAT rate under the Green Deal. They could kill all of that time they’re going to waste in dealing with that by cutting VAT wider and harder. That would deal with the structural problems in the building sector and provide incentives for growth, and it would underpin efforts like the Green Deal."