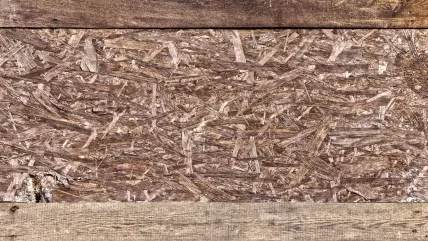
The new year is barely under way but already supply has emerged as the potentially stand-out theme of 2014,
especially given that chipboard demand is generally robust and, what’s more, is showing signs of further improvement in certain key sectors, most notably construction. Against this backdrop, January kicked off with a fresh round of price increases. For example, one UK producer hiked its raw board values by up to 10% while its T&G prices were raised by nearer 5-6% across all customer segments. In addition, "ongoing pressures" in melamine laminated products were likely to lead to "some upward movement" when price negotiations were conducted with individual customers over the coming period, a spokesperson said.
Another producer will introduce raw board price increases of 12-15% for the distribution sector by the start of February. Given current market conditions, said a spokesperson, another increase could certainly be envisaged "before the summer". Also for the distribution side, the same producer upped its melaminefaced chipboard (MFC) prices in the final quarter of last year and, at present, is anticipating the next hike will take place in April.
For both raw board and MFC, he added, sales prices into manufacturing would be subject to individual customer negotiations. Price increases were introduced following what one producer described as a "fairly strong" end to 2013 in terms of both the chipboard order book and volumes going out the door. Thanks to the significant improvement in the market during the second half of 2013 in particular, the same spokesperson believed that the year as a whole had probably witnessed records for the business; chipboard revenues had been around 15% higher year on year while sales volumes had also bettered 2012 levels – albeit to a lesser extent, he added.
The healthier sales momentum in the UK appears to have been carried over into the new year. According to a domestic producer, there has been "a lot of interest" from the shopfitting area and demand from the furniture industry has remained "quite strong". And as would be expected, he added, many customers – particularly on the merchant distribution side of the business – have been looking to rebuild stocks in the early days of 2014 after having run down their inventories immediately prior to Christmas.
However, the same contact described demand from the construction sector as "more of a mixed bag", with some distributors busier than others. As a general rule, he added, newbuild suppliers had performed better than those more focused on the refurbishment sector. Overall, however, there are grounds for more confidence with regard to construction market prospects. Norbord, for example, draws attention on its website to NHBC figures showing that the number of new homes registered between September and November last year was around 30% higher than in the same period of 2012.
While shopfitters and kitchen manufacturers among others were continuing to lodge healthy orders for chipboard, "the main impetus" for demand in the UK was now coming from newbuild, another producer agreed. Demand was "good all round", including for raw board, MFC and T&G, he added. As indicated above, the improved level of chipboard demand has brought supply issues into sharper focus. According to an established supplier into the UK market, problems with availability of chipboard were apparent in the final couple of months of last year, with "shortages" in certain thicknesses and qualities. As a result, customers "were paying a premium to get product at short notice". There has been no change in market conditions since then, he added.
However, he also said the shortages did not extend to MFC despite strong demand for this material, including a recent upturn in orders from kitchen manufacturers.
A domestic producer said its business had arrived at the Christmas break "with the lowest stocks for many years". Even though production was maintained over Christmas, inventory was still "30% lower than it would normally be at this time of year". Managing the resource would be key to the business in 2014, said the company, so it was rationalising product offering to run machines more efficiently, although still planned to introduce new lines during the year.
A fellow UK producer said current shortages were partly the result of moves to boost capacity in order to cater for the strengthening domestic demand. His own business had shut for line improvement work in September last year and was planning another stop before the end of January to help further extend output capabilities.
Imports increase
With chipboard demand returning to something like pre-downturn levels, UK production is well shy of satisfying the domestic requirement. Imports have been rising to fill the gap, with latest Timber Trade Federation statistics showing that incoming volumes jumped more than 36% in the first 10 months of last year to 480,000m³ from 352,000m³ in January-October 2012; imports from France, Portugal and Spain leapt by more than a third while double-digit percentage increases in volumes shipped to the UK were also recorded by Germany, Belgium and Ireland.
However, a question mark hangs over whether imports will continue to keep the UK market in balance: the increase in volumes purchased from other European countries "has been made possible by lower demand in their home markets", TTJ was told. "But as those markets too start to recover, will they keep the same appetite for exporting chipboard?" Another factor, he added, was that wood supply represented a significant challenge in mainland Europe.
Another contact said: "Taking into consideration some of the [Continental] factory closures in 2013 and more to come in the near future, we can foresee that chipboard availability will not improve." And a UK producer was equally blunt: "I cannot see that we can rely on imports."
Rising costs
However, this swing of the supply/demand pendulum is not the sole justification for rising chipboard prices in the UK. Domestic producers are under pressure from mounting costs and also from the need to show an improved return on investment, especially during a period of decent demand and limited availability.
Thanks in part to the continuing impact of biomass on supply, he anticipated "double digit" percentage increases in wood costs on 2013. A fellow producer also predicted timber costs "will keep going up" this year, noting too that his methanol bill had now jumped 26% year on year. As relayed in TTJ’s final chipboard report of 2013.
Egger UK is planning to invest £10-12m in new technology for the impregnation lamination area of its Hexham facility, one of the results of which will be some increase in capacity. Initially pencilled in for the second half of 2014, the project is now more likely to be undertaken in the first quarter of 2015 in order to allow for a build-up of stocks over the Christmas period to help offset the production that will be lost during the short period of downtime required to install the new technology, a company spokesperson said.
Such investments underline the growing confidence in the UK chipboard sector. But although one producer welcomed "signs that this is actually going to be a more positive year than 2013", he also expressed the hope that any improvement would be gradual rather than dramatic and that "peaks and troughs" would be avoided. Such volatility would only exacerbate inevitable supply issues, he added.