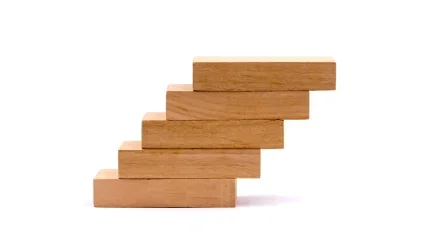
Koppers is a leading producer of cuttingedge timber treatment products, focused on making the timber industry more sustainable and making timber a safer, more durable material across a range of different applications. But we don’t magic them out of thin air; they result from years of careful product development and production at sites such as our Darlington plant.
We work on four main product streams at Darlington – low-pressure and highpressure treatments, coloured treatments, and flame retardant – which include a host of different individual products. Recent updates have brought part of Koppers’ research and development function to Darlington, so now as well as large-scale production the site is also crucial to the innovation that enables our treatments to play a part in making timber products better.
But to do that, the site needs to be efficient, sustainable, and compliant, and this requires our team to work around the clock on the equipment, processes and certifications we have in place. Here’s how we’re doing it, and how our Project 2025 will see the plant hit new heights of productivity and innovation in years to come.
STAYING COMPLIANT
Compliance is an existential issue for the Darlington site and for Koppers on a global level. Chemical products such as wood treatments are subject to a complex regulatory structure to ensure that they minimise risk to humans or the environment.
There are also significant differences in how timber treatment products are regulated in different territories, and for the majority that applies to products that are moving through a territory, as well as being sold and used there. For example, a product made in the UK, due to be sold in Portugal, but travelling through France and Spain to arrive there, will need to be compliant with standards in all four countries before it gets on the ferry to Calais.
Keeping ourselves compliant is the base level, but we also work towards internationally recognised voluntary standards that reflect industry best practice. These include the ISO 9001 and ISO 14001 standards for quality control and environmental management systems, which validate how we store products and by-products to ensure that they don’t contaminate one another, how we evaluate and mitigate environmental risks, and the training our team receives. These standards keep up with how the industry evolves, learns about new risks and technologies, and ensures that our processes evolve with them.
It’s not just about when everything is going smoothly – as a chemical producer, we need strict protocols in place for potential accidents at the plant. This certification, known as Control of Major Accident Hazards (COMAH), is a legal requirement and no small undertaking, because it’s not just about what we do inside the plant. It’s about how we work with local communities and emergency services to familiarise them with our operations and establish action plans that activate in the case of an accident.
ZERO HARM/ZERO WASTE
Fulfilling our safety obligations isn’t something we can do reactively – our site needs to be safe and compliant before production starts. This proactive mindset extends across every aspect of our operations, including new product development, preventative maintenance and improving efficiency – and the company’s zero harm/ zero waste culture is all about thinking forwards.
Manufacturing methods and technology have come a long way since the Darlington site opened in 1972, to the point that many of our processes are independent and our staff can dedicate their time to keeping things running smoothly, optimising workflows, and pre-empting issues that could arise in the future.
Large-scale manufacturing, and our industry in particular, have very long lead times for new products, long life cycles for machinery and long regulatory approvals processes, meaning the decisions we take now will keep having an impact for years to come. Here in Darlington, our Project 2025 will see us streamline operations and generate more space on site, with fewer larger storage tanks that free up areas for more research and development work.
STAYING SUSTAINABLE
Timber treatment is making the timber industry more sustainable, and helping timber play a larger role in the transition to a greener economy, but that doesn’t mean we can stop looking at how to reduce the impact of our own operations. One key transition that we’re making is from solvent-based to water-based treatments, a long process that began a long time ago and continues for the foreseeable, but one that is critical to future proofing our operations as our clients take a similar look at their environmental impact.
This is a long-term, large-scale change in the company’s direction that has serious local relevance for us, but we’re also driving smaller changes to make the site greener. One significant example is implementing a water management system to gather rainwater and put it to use in the production process. As part of Project 2025, we aim to scale up this capacity and manage rainwater directly on the roofs at the site.
THE LITTLE THINGS
Koppers is a global leader in the timber industry, but that whole is made up of more than 40 different individual sites, each functioning as a crucial cog. At these sites, the devil’s in the detail when it comes to ensuring what we make fulfils our regulatory responsibilities, has the right impact on the people and the environment, and keeps pace with a fast-moving sector.