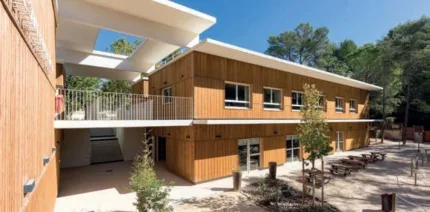
PiveteauBois has big ambitions for its wood composite range, including in the UK.
One of France’s leading softwood sawmillers, it has been making its Sylneobrand product for the cladding, decking and other outdoor products markets for 20 years. In that time demand has grown exponentially. It now sees it further increasing momentum, appealing to customers who want a woodbased, wood-look product combining durability with ultra-low maintenance. Environmental validation and fire safety, says PiveteauBois, are adding to its products’ impetus.
Sylneo is made at the company’s Sainte- Florence headquarters site south of Nantes. It’s produced by extrusion combining softwood residues from its sawmills with a mix of end-of-life recycled polymer from such products as windows and piping, plus coupling agents, dye and anti-UV additives.
“The boards comprise 60% softwood, which is PEFC-certified, and 40% partly recycled polymer,” said Sylneo head of sales and marketing Matthias Rolland. “The end result is a hard-wearing, shock resistant board that does not split or break. Sylneo is solid and homogenous and so does not require finishing at board ends, saving on material and labour, and it offers much better stability than hollow boards. It is also guaranteed splinter-free.
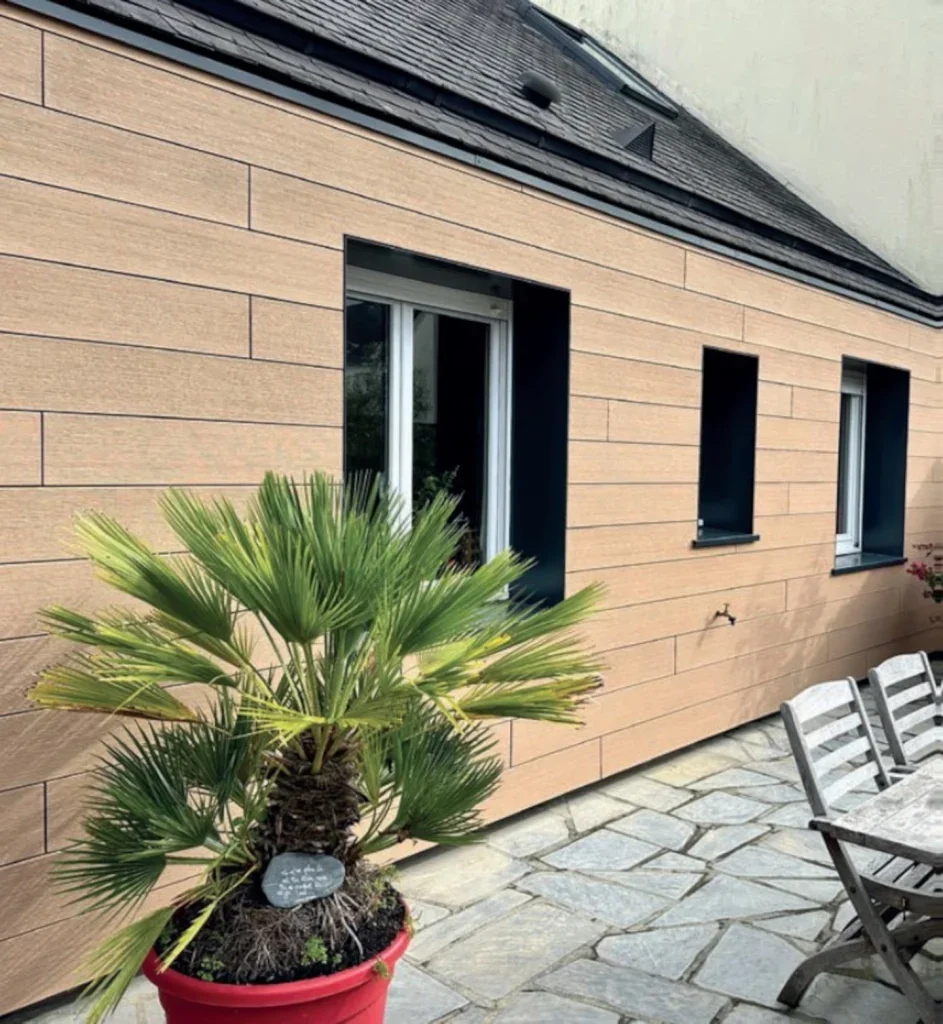
“The range additionally includes decking, which even when wet, provides a non-slip surface. Sylneo is virtually impervious to humidity and not affected by chlorine or salt so is suited to seaside and poolside applications. It’s covered by our 20-year warranty against insect damage, white decay and soft rot and the only maintenance needed is washing with water using a hard brush.”
He added that, as the Sylneo decking is made with polypropylene rather than the polyethylene used in some of the best-known wood plastic composites, it’s denser.
“Polypropylene is also used, for instance, to make car bumpers,” he said. “It gives us several advantages. It means the boards are more resistant to scratching, are naturally resistant to stains, and allow a longer centre distance for joists. They are more heat resistant and give a more natural aesthetic.”
FIRE RESISTANCE CLASSIFICATIONS
Sylneo cladding is supplied in various fire resistance classifications, from Euroclass D (the minimum) to Euroclass B. The higher ratings are achieved through the inclusion of fireproof additives into the raw material mix. And the products’ certified fire resistance has led to their use in large scale building projects.
Quality control testing is undertaken to European standard WPC EN15534-5 by the French Technological Institute for Forest Cellulose Wood-Construction & Furniture (FCBA). It covers colour retention over time, mechanical strength and moisture take-up.
“Batch testing is also performed twice every eight hours, which means that each pallet is tested a minimum of once and sometimes twice,” said Mr Rolland. “These tests cover product dimensions – length, thickness, width – weight per metre, density, colour measurement, a three-point flexural test and e-modulus and stress at break. In addition, once a week, a boiling test is performed per product type and extrusion line.”
The dimensional stability of Sylneo meets the BS EN 15534 standard.

Besides using certified wood residue and recycled polymer, PiveteauBois cites among Sylneo’s environmental credentials the fact that, at the end of its service life, it can be ground down and used to make new composite boards. It’s also accredited to the French HQE (High Environmental Quality) green building standard. This sets criteria for such aspects as waste, energy, and pollution minimisation in production, maintenance reduction in use and recyclability.
It has approvals too from ADEME, the French Environmental and Energy Management Agency, and, says PiveteauBois, meets circular economy product requirements.
“We also have an FDES, Environmental and Health Declaration Sheet for Sylneo,” said Mr Rolland. “This is a standardised document which presents the results of life cycle analysis of a product, as well as health information, so the environmental and health performance of a building can be calculated as part of its eco-design.”
Sylneo cladding is made in two variants, shiplap Malo and false open-jointed Nova. It comes in 10 colours and five surface finishes. Besides cladding and decking, PiveteauBois makes fencing and exterior screening products in the same material.
The company also, of course, makes solid and engineered timber cladding and sells its grey and brown pressure treated laminated Douglas fir range in the UK. It does see Sylneo as providing an alternative to wood products for some customers, but it also bills it as competitor for other man-made material cladding.
“We’re offering an alternative to customers who want the warmth of wood and a wood effect without its natural constraints, but it is also an alternative option to products such as PVC or fibre cement cladding,” said Mr Rolland.
Pricewise, Sylneo is described as on a par with timber cladding in such durable hardwoods as cumaru and ipe and also western red cedar.
As for routes to market, PiveteauBois aims to mirror its French wood plastic composites sales model in the UK.
“In France we work through distributors on the one hand, and industrial clients on the other,” said Mr Rolland. “We are looking to develop the UK market in the same way but are open to any development opportunities.”
The company is positive about Sylneo’s prospects in the UK.
“Demand for wood plastic composites is increasing, and having Euroclass B fire classifications gives us an additional competitive edge in the UK, enabling us to stand out from products already on the market,” said Mr Rolland.
PiveteauBois sees potential for growth elsewhere too, he added.
“We are looking to develop our wood plastic composites sales more widely across the rest of Europe in coming years,” he said. “It’s also our ambition to open a new factory in 2026, which will double our 250,000m2 annual capacity.”