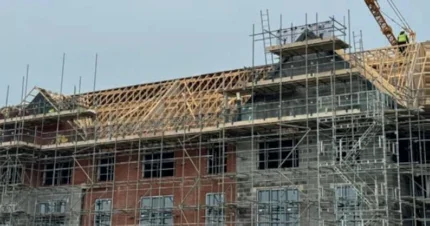
In the small village of Welton, Lincolnshire, Acorn Timber Engineering Ltd took on what might be one of the most ambitious trussed rafter roof projects the UK has seen.
Welton Extra Care Apartments and Bungalows is a development aimed at providing affordable housing for those over 55 – but for Acorn, it was an opportunity to push the limits of timber engineering.
The Extra Care Scheme, comprising 62 apartments and 10 bungalows, initially came to Acorn Timber Engineering through RG Carter (Lincoln) with a request to supply metal web joists for the flat roof links between the site’s four main blocks.
But Simon Copley, who heads the team at Acorn, saw more potential. Instead of sticking to the brief, he pitched for the entire roof structure, covering both the apartment building and the bungalows. It was a bold move for the company, and it paid off.
The project ultimately spanned nearly 3,500m2, requiring Acorn to manufacture over 2,500 components, including trusses, panels, and posi joists. The team believes this might be one of the largest single-trussed rafter roofs built in the UK in recent years.
Managing a roof structure of this size came with its challenges. The team had to use a base-and-cap system to stay within transport height limits while ensuring everything would line up perfectly during installation.
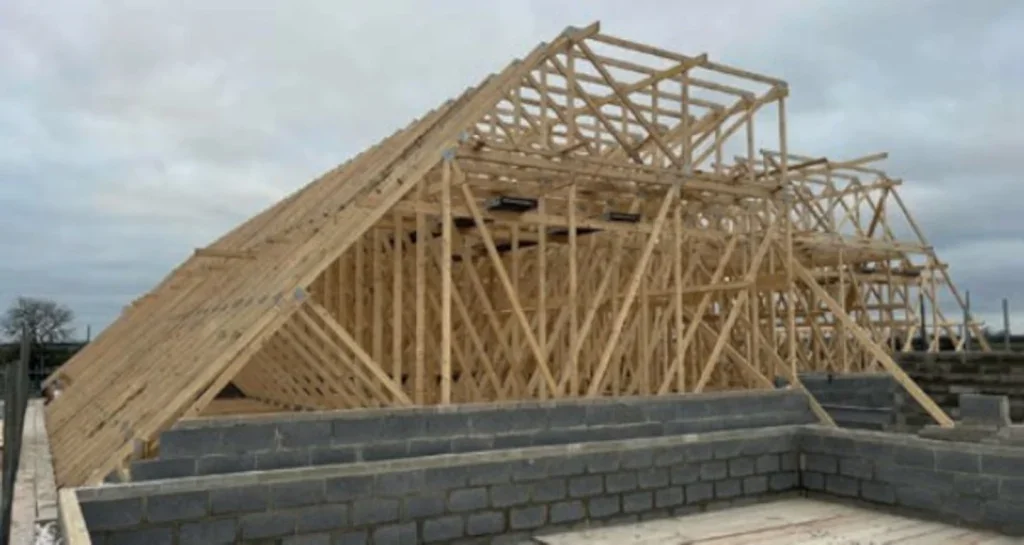
The trusses were designed with special attention to web alignment to make the bracing pattern as straightforward as possible – a small detail that made a big difference.
The team also had to juggle logistics on-site.
“It’s not just about putting up a roof; it’s about making sure every piece fits perfectly while keeping the process efficient,” explained Mr Copley.
The scale of the trusses meant that safety was critical throughout the project.
Mr Copley’s plan involved installing the base trusses first, creating a sturdy platform for the workers to assemble the cap trusses. They also pre-cut large spandrel and gable panels into smaller sections in the factory to make handling safer on-site.
A crane was permanently stationed onsite to manage the heavy lifting, ensuring everything went up smoothly and safely.
MINIMISING ENVIRONMENTAL IMPACT
Acorn Timber Engineering isn’t just about size – it is also committed to minimising its environmental impact. All timber used in the project was PEFC-certified, ensuring responsible sourcing.
The team maximised stock length usage to cut down on waste, and it optimised truss sizes to fill each lorry load efficiently. Fewer trips meant a lower carbon footprint, which was a win for both the company and the environment.
“Breaking down the project into smaller sections was crucial,” said Mr Copley. “We needed to stay flexible, so we timed the truss drawings with the build schedule, making sure we weren’t holding anything up. We batched the trusses in stages, which kept production moving efficiently through the factory.
“We’ve been using MiTek’s Pamir software for a while, but a project of this scale forced us to dig deeper into its features. It was a learning curve, but it paid off in the end.
“We came out of it not just with a finished roof, but with a better understanding of our capabilities and the tools we use.”
The effort that was put into the project didn’t go unnoticed. The project received high praise at the Roofscape Design Awards, where the judges commented:
“Excellent application with detailed and appropriate information provided. Impressive scale with the technical and logistical challenges that were brought due to the size of the trussed rafters. This project needed numerous design solutions to achieve the overall design that was achieved with excellence.”
Welton Extra Care Scheme is a reminder that even in a small village, big things can happen. Acorn Timber Engineering took a chance, delivered a massive project, and learned a lot along the way. For Mr Copley and his team, it wasn’t just about building a roof; it was about testing limits and setting a new standard for what’s possible in timber engineering.