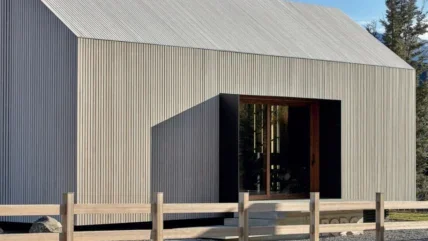
Plantation-grown New Zealand radiata pine ranks among the most renewable timber resources. It’s fast-growing and cultivated on an impressive scale – and it’s what’s used to make Abodo Vulcan, the thermally modified wood that’s internationally established in cladding and decking markets and making increasing inroads into joinery.
Abodo was formed in 2001 and remains a family-owned timber business, led by brothers Daniel and Nathan Gudsell. They started thermally modifying wood 15 years ago, with the two-fold objective of offering a durable alternative to chemically treated softwood and less abundant hardwoods and to make more of New Zealand’s plentiful supply of radiata pine.
“There was increasing awareness that a durable, sustainable, environmentally benign product was needed, particularly to substitute timber processed with such treatments as copper chrome arsenic, but also hardwoods from old-growth forests, where there is more limited supply and in some cases question marks over sustainability,” said Lewis Marshall, Abodo UK area manager. “There was also a desire to add value to radiata pine in New Zealand and especially to develop the export market for further processed products rather than just logs.”
The focus on exports particularly was understandable given New Zealand produces three times as much radiata pine timber as it consumes domestically.
The country’s plantation forests cover around 6% of its land area, a total of 1.8 million ha. Of that, 90% is planted with radiata, with trees being ready for harvest at 27 years.
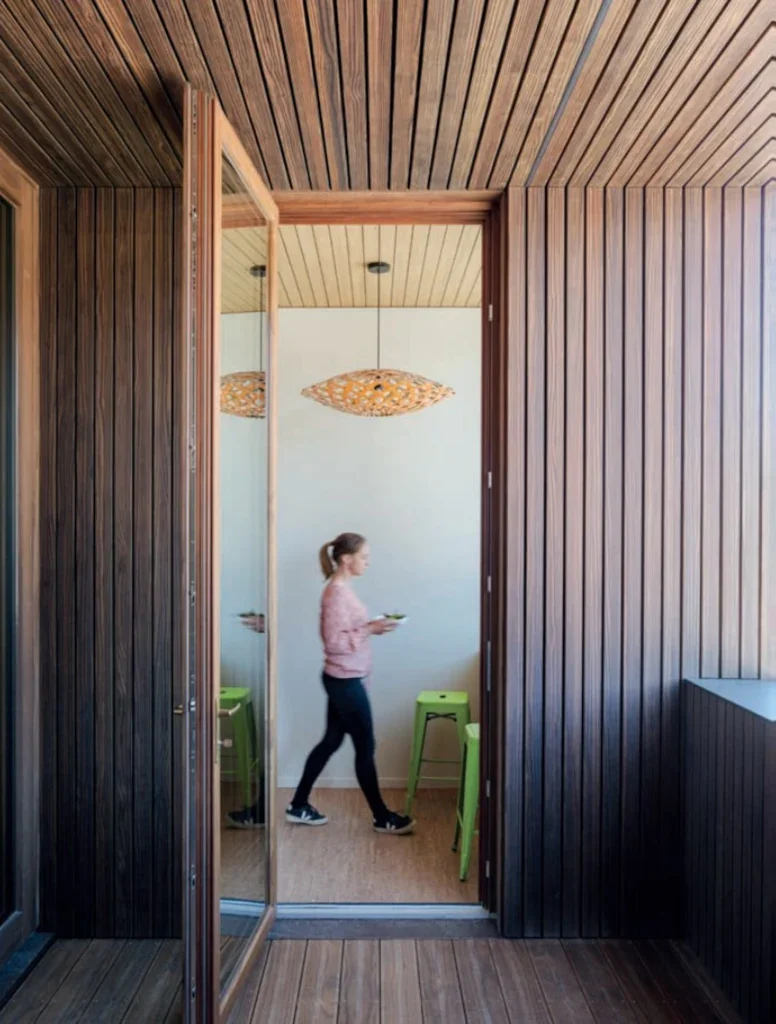
For some, the term plantation forest conjures the image of a sterile monoculture, supporting single tree species and little else in the way of wildlife and other flora. But Abodo says planted pine forests can provide long-term ecosystem benefits, not just timber, and a place for recreation, but also carbon sequestration, water regulation, and soil stabilisation.
“Most of our wood comes from the Kaingaroa forest in the central North Island, one of the largest man-made plantation forests in the southern hemisphere,” said Mr Marshall. “It is all FSC-certified and the plantation managers are committed to supporting biodiversification and to land and soil conservation. Well-managed planted forests can maintain or even improve soil health while supporting a diverse range of organisms, plants and animals.”
The company was not, of course, the first to thermally modify softwood, with Finland pioneering the process in the 1990s.
“When the company was looking at ways of increasing radiata pine durability, chemical-free thermal modification stood out for us. And we acknowledge that the Finns led that space. However, we adapted the process specifically for radiata pine,” said Mr Marshall.
The Finnish method is largely used on European pine and spruce. These are respectively durability class 3 and 4 and are heated to between 190°C and 212°C to achieve a structural change at cellular level that increases moisture resistance and to degrade the wood’s hemi-cellulose, on which fungi feed. The end result is hardwood equivalent durability.
“We took this approach and came up with our own specific schedule as radiata pine is durability class 5,” said Mr Marshall. “We ramp up the kiln temperature to 230°C, with the heat penetrating the wood at about 1mm per hour. Once the core is at 230°C, it’s held at that for a minimum of two hours. The moisture content at this stage is essentially zero. After this, the timber is slowly cooled, then reconditioned with steam, raising moisture content to a target of 6-7%. It will then remain at this equilibrium and the timber is transformed from durability class 5 to class 1.”
Abodo has developed the largest testing data suite for thermally modified radiata pine performance and submitted this to BM TRADA for evaluation. The company provides a 15-year ‘Built to Last’ warranty for its timber against all forms of fungal decay and BM TRADA concluded that, in uncoated form, it has an expected service life in above ground external applications of 30 years. Coated, this rises to 60 years.
To achieve the accuracy required, Abodo starts its thermal modification process using diesel to heat its kilns.
“Then, during the process, resins and other extractives come out of the wood and the residue is extracted to become an additional fuel for the boiler. The result is a self-fulfilling energy cycle,” said Mr Marshall. “The current process also gives us the opportunity to reduce our carbon footprint further with the future goal of using biomass to fuel the kilns.”
Using its current kilning approach, he added, Abodo’s thermally treated timber has still sequestered twice as much carbon per kg than is emitted in the production process and in transporting the finished product to Europe.
“Radiata pine is very efficient at sequestering carbon, absorbing 20 tonnes per hectare per year compared to Siberian larch’s 1.4 tonnes per hectare,” said Mr Marshall. “We acknowledge that, for carbon footprint reasons, there is a growing trend to local sourcing of materials, but with our products, you can have a product that is sustainably sourced, durable and still carbon [positive] when you ship it halfway around the world.”
Moreover, he added, “Abodo’s products are backed by an EPD validating its carbon and wider environmental profile since 2018.”
Besides being class 1 (EN350-1) and naturally durable, Abodo’s timber has enhanced dimensional stability. Comprising clear pruned radiata, it gives knot-free long lengths, and its thermal properties are also improved by 20%, achieving a lamda value of 0.095W/(mK).
“That adds to its value for door and window-making and compares with 0.12 for acetylated pine and 0.16 for sapele,” said Mr Marshall.
The wood is a homogenous brown through its thickness. “It can be left uncoated, in which case it will silver off quickly,” said Mr Marshall. “But it is also ideal for coating with opaque and pigmented finishes, with the removal of 60kg/m3 of extractives during thermal modification minimising risk of bleed-through.”
Abodo’s timber is marketed and supplied in two variants, Vulcan-Flat Sawn and Vulcan- Vertical Grain. The former is as described and sold in 25mm/32mm/38mm/50mm thicknesses, in a variety of widths between 100mm-200mm.
Vulcan-Vertical Grain is a laminated engineered product comprising typically of five or six lamellas. Main stocked sizes are 146x147mm or 192x200mm.
“For Vulcan-Vertical Grain, we take the flat sawn timber and face laminate it into blocks, which we resaw through the glue lines to create the finished engineered vertical grain material,” said Mr Marshall. “It’s our flagship product, giving enhanced dimensional stability – 2% tangential swell, as against 3-4% for flat sawn timber. It’s also less prone to checking. It was developed initially to rival old growth western red cedar and customers are drawn by the vertical grain aesthetic.”
In terms of price point, Vulcan-Flat Sawn is described as “sitting close to the likes of sapele” and Vulcan-Vertical Grain “to the likes of Accoya”.
Abodo initially targeted exterior feature products markets, with its timber proving particularly popular for cladding and decking, but also for pergolas, fencing and other garden products. Around 10 years ago it started to be taken up by joinery producers too, particularly Vulcan-Vertical Grain, and it has gained momentum in the market since.
“Joinery users comment on the dimensional stability,” said Mr Marshall. “Given that the thermal process reduces the density from 480kg/m3 to 420kg/m3, it is also easy to handle. Joiners have to take account of the lower density in working the timber, but they report that it machines beautifully using the correct tooling sharpness, cutter and grinder angles. We recommend use of freshly ground knives at 20° with the result that less sanding and prep work is required after machining.”
Abodo’s Vulcan timber first came on to the UK market about 10 years ago. Glenalmond became a distributor targeting the cladding, decking and other outdoor products markets, while Russwood became Abodo’s architectural partner.
Abodo now sees significant opportunity for growing momentum in the country.
Mr Marshall, who moved to New Zealand from the UK aged 10 with his family and has worked for Abodo for five years, moved back to become UK area manager mid-2024.
“My role is to provide technical support and educate architects, builders and end users with any issues and to help them out on the ground. We’re not just offering a product, but day-to-day back-up for it too.”
In another strategic move, in 2023 Abodo signed a distribution agreement with Timbmet too, with a particular focus on the joinery market.
“The UK joinery sector is pretty hardwood heavy, but we are getting a lot of positive feedback about our products, particularly for use for windows and exterior doors, but also interior applications,” said Mr Marshall.
Abodo is also supporting its distributors with pull-through marketing.
“For instance, we are providing monthly CPD webinars for architects, providing an educational platform to share ideas about product use and to generate brand awareness,” said Mr Marshall.
Abodo is positive about its prospects in the UK and the wider international market – it also exports to mainland Europe, Australia, Asia and the US.
“The construction sector is increasingly looking to use more wood to reduce its carbon footprint and it’s looking for a sustainable, durable timber that delivers high performance low environmental-impact products,” said Mr Marshall.
Another reason for optimism, he added, is that New Zealand radiata pine is set to become more abundant still, with the plantation sector engaged in research to boost forest yield. The target is to increase it from 28m3/ha per year to 40m3/ha by 2040, by using the same existing 6% land mass and focusing on planting the right trees in the right place and “optimising the forests”.
Abodo has its own plans for growth too.
“We currently have four kilns and are producing 30,000m3 of rough sawn timber a year,” said Mr Marshall. “The target is to double that output in four years.”
TIMBMET CONFIDENT IN ABODO
Timbmet managing director Nigel Cox said the company took on distribution of Abodo’s Vulcan sawn and laminated thermally modified timber after being impressed by both its technical and environmental performance.
“Abodo’s technical knowledge, supported by test evidence, gave us confidence in a product offering an alternative to a red hardwood product,” he said. “The material also has strong environmental credentials. It’s ethically sourced, low carbon and all FSC certified.”
Abodo’s products, he added, have the benefit of a strong support team in the UK and New Zealand. Working with them, Timbmet is targeting the range of markets and customers.
“Architects and other specifiers are being met to promote the products’ credentials and joinery section sizes are being targeted to companies for a range of uses including window, door, general joinery and gate manufacture,” said Mr Cox. “The full range is available to merchants, including sawn timber or vertical grain block cladding, which is also being targeted at installers and end users.”