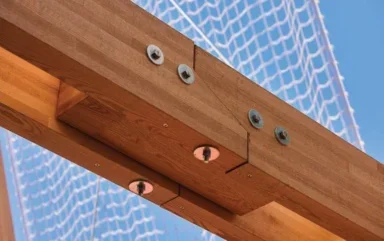
The creation of Vert for this year’s London Design Festival (LDF) is a two-fold story of achieving environmental positives in our over hectic, overheating urban centres. One aspect is about what Vert does, the other about how it’s made and crucially what it’s made of.
Fundamentally Vert is about urban greening, bringing natural havens into our town and city spaces. It is effectively a giant – 10m x 10m x 10m – demountable pergola, a frame supporting hemp netting up which can twine fast-growing plants, bedded in planters and specifically chosen for their resilience and wildlife appeal.
The result is an oasis of green that can be set up in areas where it’s impractical to plant trees and other greenery. It provides habitats for insect life and consequently a food source for birds and other animals. For human urban dwellers it creates an area of welcome shelter, shade and daily contact with nature, with the well-being benefits that has been shown to bring.
Coming up with the Vert concept was a joint endeavour of German industrial designers Diez Office (DO) and urban greening specialists OMC°C. The third lead partner in developing the project and bringing it to this year’s LDF was the American Hardwood Export Council (AHEC), which introduces that other critical element, the material Vert is constructed in.
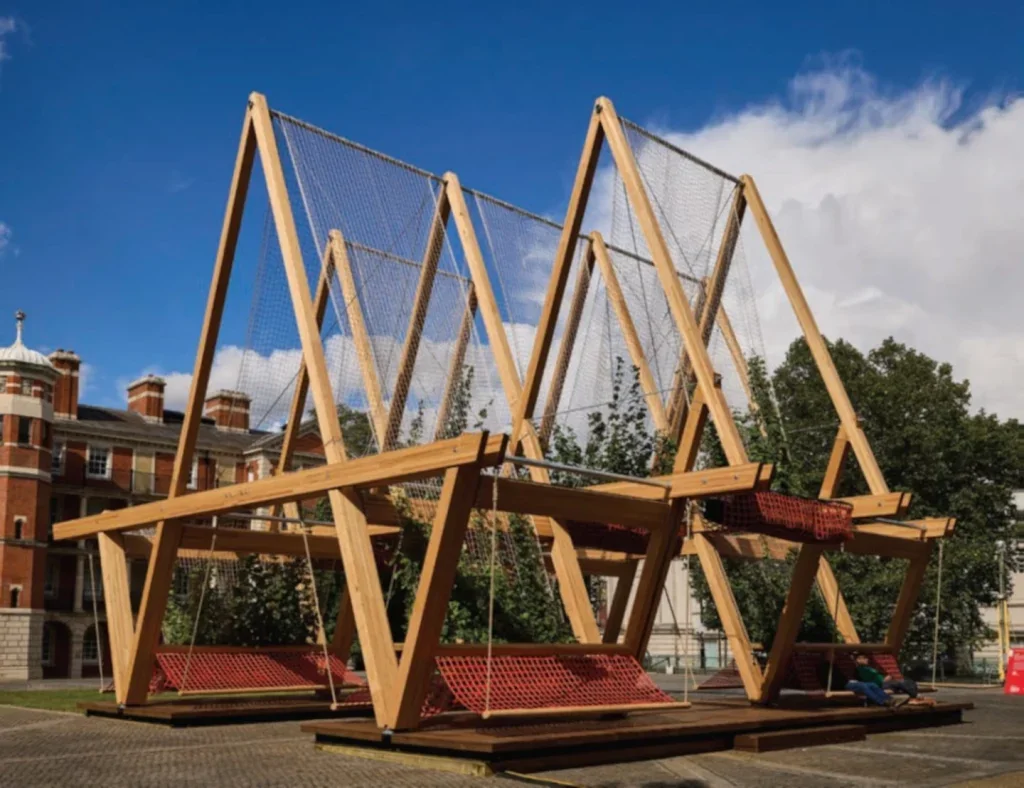
AHEC’s role is to develop the market for US hardwoods. That includes supporting projects that broaden their range of applications. At the same time, while growing use of these timbers, with all the carbon and wider environmental benefits that can bring to manufacturing and construction, the aim is ensuring the long-term resilience of the forest resource.
In recent years, the European market has homed in increasingly on a handful of US hardwoods, a fashion trend which has bred familiarity and perhaps a reluctance to try something different. But, says AHEC, for the long-term future of the forest, the biodiversity it supports and its wider environmental values, we must use the full spectrum of species. Using a favoured few risks putting these under supply stress, not to mention limiting overall hardwood availability and market choice. It is increasingly recognised that we need to use more timber and fewer energy intensive, high embodied carbon materials to help combat climate change. But it has to be sustainably sourced. That, says AHEC, means using what the US hardwood forest sustainably provides. It means working in tune with nature.
Vert brings these strands together. It is constructed in red oak, one of those US species that is less widely used in Europe, yet is hugely abundant, comprising 18% of the US hardwood forest. Moreover, it is red oak in an engineered, or mass timber format – glulam.
AHEC initiated a previous LDF installation trialling red oak glulam. Timber Wave comprised a web of slender laminated, fingerjointed elements creating a curving portal around the entrance of the V&A museum. Vert, which was on site at the Chelsea College of Arts from the start of this year’s LDF to October 14, pushes the product’s technical boundaries and highlights its structural potential still further.
Helping bring this aspiration to reality were three other members of the Vert team. These were pioneering engineered wood developers and fabricators Neue Holzbau (NH) of Switzerland, German structural engineer and partner on previous OMC°C projects Bollinger + Grohmann and London architects Forward Studio.
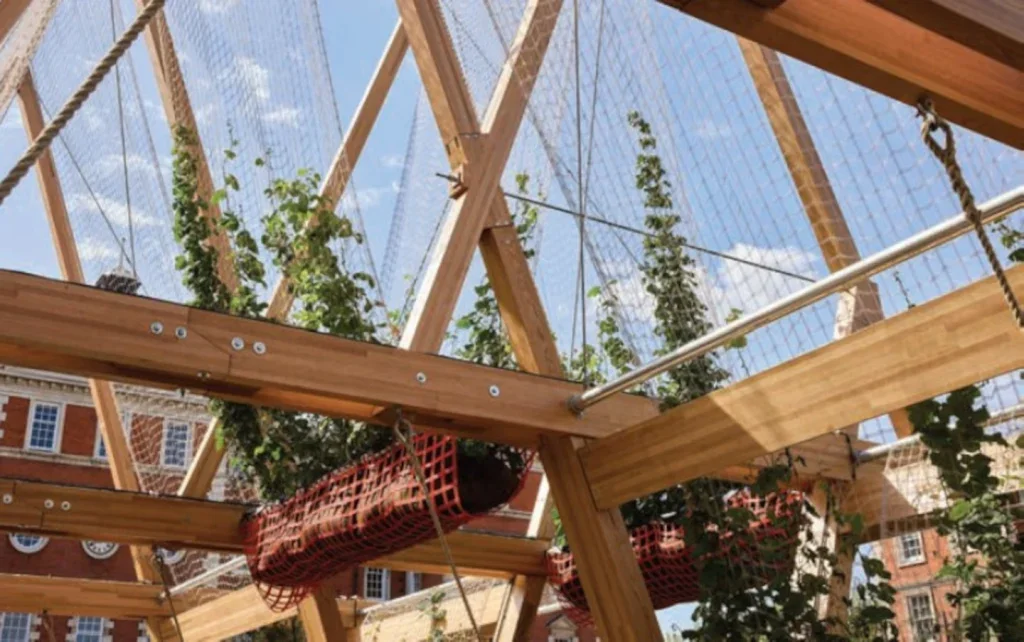
Neue Holzbau brought its extensive experience in developing new engineered wood solutions to the project.
While the bulk of engineered or mass timber is in softwood, NH also has extensive experience in using hardwoods.
“Hardwood has been integrated in our production as standard for nearly 20 years,” said CEO international business Reto Schneider. “We bond beech, ash, oak and many other speciality woods.”
Making engineered timber products in hardwood rather than softwood enables manufacturers to work more materiallyefficiently, given its higher density and strength to weight.
“We can use smaller cross sections in the supporting structure and produce very efficient, material-friendly components,” said Mr Schneider.
Forward Studio founder Fred Pittman worked with AHEC on the Timber Wave while at AL_A architects. Working with DO on Vert, he contributed his architectural perspective and advised on such issues as buildability and after-use. He agreed with NH on the attraction of using hardwoods for engineered wood, notably the opportunity they give for using less timber to do more.
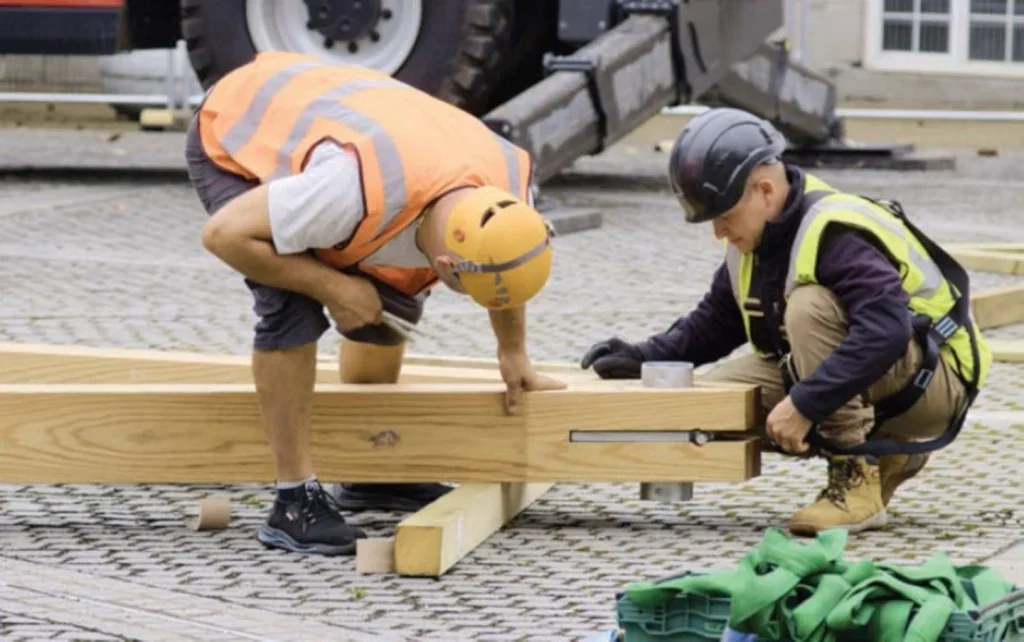
The bulkiness of softwood engineered wood products, he said, can be a deterrent to specifiers.
“In large, hangar type buildings, it may be less important, but in an office or school classroom, those extra centimetres can count,” he said. “Working in hardwood allows for finer section sizes and a lighter structure. It adds a different dimension and is also visually richer. NH showed us two glulam columns rated for the same kN force, one hardwood, one softwood – the difference in section was eye-opening.”
The fact you don’t need as much timber, also narrows the price differential between hardwood and softwood engineered timber said Mr Pitman.
NH used the same type of adhesive for red oak glulam as for other hardwoods, but “adapted certain parameters” to suit the species. “The aim was to develop a solution enabling red oak glulam to be produced in an industrial way,” said Mr Schneider.
NH has its own laboratory, but in developing red oak glulam, it also involved researchers at Bern University of Applied Sciences.
“We wanted an external viewpoint from an accredited laboratory and an official report on the product’s properties,” said Mr Schneider.
The red oak was tested alongside NH-made glulam in US white oak, tulipwood, European oak, plus thermo-treated red oak. In the finger-joint tensile strength testing under standard EN408, tulipwood performed best at 39.5 N/mm2, followed by red oak at 34.6 N/mm2, white oak at 31.9 N/mm2 and European oak 30.4 N/mm2.
While heat treatment makes timber more durable and particularly suited to exterior use, it also makes it more brittle. Consequently, all samples of the thermo-treated glulam failed below the minimum test time.
In delamination tests all tulipwood glulam specimens passed. The red oak and the thermally modified red oak had one failure at the 30-minute closed time but passed at a closed time of 60 minutes. European oak passed one test at the longer time while white oak failed at both times, a fact attributed to its lower density.
NH was impressed.
“As well as bonding and pressing pressures, tests covered the behaviour of the joinery and performance of joining technologies and the red oak surprised everyone,” said Mr Schneider. “It performed significantly better than both European and US white oak.”
The finished Vert structure is on quite a scale. The planting actually starts 3m above ground so people can walk underneath, then extends to the full 10m height of the framework. Engineering the structure so that it fulfilled its urban greening purpose most effectively and was at the same time hugely stable, was a demanding process said Bollinger + Grohmann’s Frankfurt director Philipp Eisenbach.
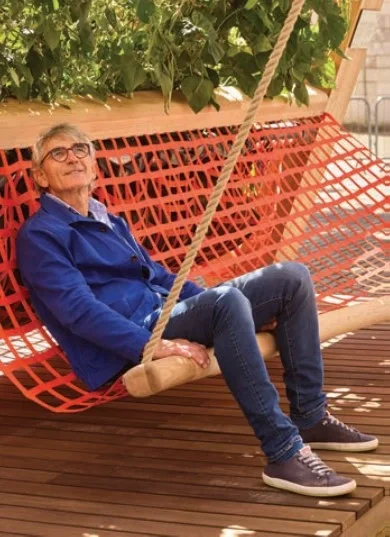
“In the planning phase, our focus was not just to use sustainable materials but achieving material saving,” he said. “We also designed the structure for simple assembly and nondestructive disassembly to allow multiple use and increase the structure’s lifespan. At the same time, we had to guarantee structural stability.”
During the concept phase, the structure was analysed in a parametric environment to evaluate its behaviour while manipulating aspects including height, width, and the number and size of the planting nets. The result, said Mr Eisenbach, is a structure that is efficient and safe.
To facilitate ease of disassembly, the structure is secured to steel base plates rather than any more invasive foundation. As for the red oak glulam elements, the base V columns comprise 360mm x 190mm sections, the horizontal double beams are 380mm x 110mm, horizontal beams 400mm x 190mm and A-Frames 190mm x 190mm.
The timber is connected using NH’s GSA joint system in galvanised steel.
“This is an in-house developed system we’ve been using over 20 years,” said Mr Schneider. “It comprises glued in threaded rods that allow maximum loads to be passed through small timber cross-sections.”
The glulam is finished in a Saicos waterbased impregnation and UV coating, while the deck, in thermally modified red oak, is left unfinished.
“Due to the structure being outdoors and use of galvanised steel connections, NH says a structural engineer should check Vert before reuse after two years,” said Mr Pittman. “But it’s anticipated the timber would last far beyond this.”
As for the longer-term future of red oak glulam, partners in the Vert project see it being employed in a wide variety of structural applications.
“You can see its application in office buildings with British Council for Offices structural grids from 9m to 15m,” said Mr Pittman. “There are also possibilities in industrial architecture, urban infrastructure, schools, sports, and hospitality projects.”
NH also sees “great untapped potential”.
“We were all pleasantly surprised by red oak glulam’s quality and performance and the finish is marvellous,” said Mr Schneider. “And as we only have one planet, we must take care of the wood resource and use those species that occur in large quantities. Following Vert, we want to discuss the next steps with AHEC to take our red oak progress further.”