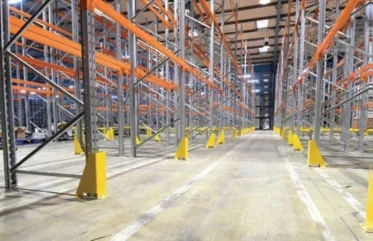
Every business owner and director knows they have a responsibility to provide good governance, manage employee rights and protect from health and safety risks in the workplace.
The latter can be difficult when working in environments such as timber yards and manufacturing units where there can continually be risks from trips and falls and constant movement of vehicles and employees. To provide guidance, there are numerous Health and Safety Executive (HSE) documents in place such as the Health and Safety at Work Act and Manual Handling Operations Regulations that provide guidance on the correct steps.
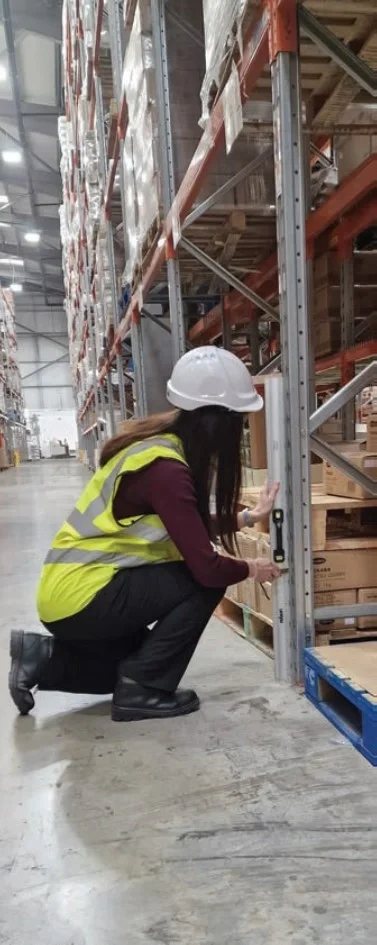
What those working in the industry might not realise is that there are similar regulations in place that apply to storage equipment such as racking and shelving. Storage equipment like racking and shelving plays a vital role within the timber industry, helping businesses to run efficiently and maximise opportunities. Once in place and doing its intended job, it is easy to put racking consideration to one side. In reality, there are multiple factors that determine whether it performs correctly and safely.
As a leading voice in the storage equipment industry, the Storage Equipment Manufacturers Association (SEMA), wants to advise the timber industry on the correct steps when meeting racking safety regulations.
WHAT REGULATIONS COVER RACKING?
As a multi-faceted environment, there are several HSE documents that directors should be aware apply to racking. These include guidance such as the Health & Safety at Work Act 1974 and Provision and Use of Work Equipment Regulations 1998 (PUWER) which cover taking the correct steps to ensure work equipment like racking is maintained appropriately, with information and instruction provided on safe use. While these guidelines offer general advice on looking after your equipment, they don’t go into detail on how to apply safety measures to racking equipment.
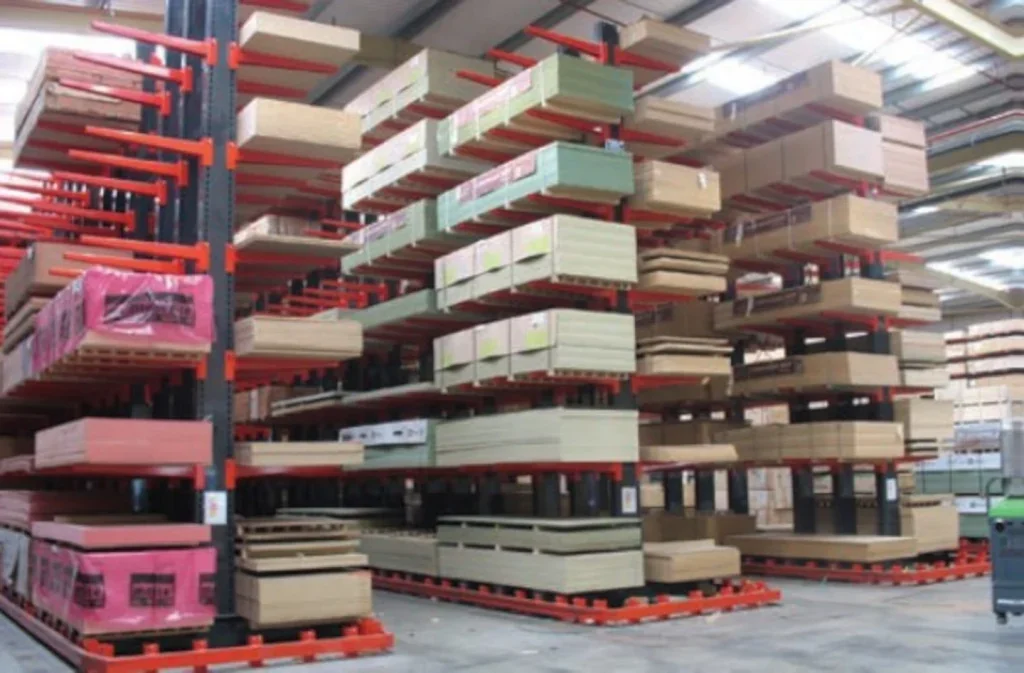
Anyone who has racking at their site should also reference, in conjunction with the above, HSG76 Warehousing and Storage: A Guide to Health and Safety. This HSE guidance document specifically relates to racking structures and covers the lifespan of the equipment, from the initial design, supply and installation right through to looking after the racking. The document also covers manual and mechanical handling, site transport, working at height and emphasises warehouse owners’ responsibilities to ensure best practice and general prevention to avoid risks and hazards.
The second important guidance documents are SEMA codes, which are critical to ensure products are designed, installed, maintained and repaired in line with quality standards and safety requirements. These codes are specialist, but the purpose is simple, to make sure racking users can have a reasonable level of confidence the equipment will meet its intended purpose.
HEALTH AND SAFETY STEPS TO CONSIDER
It is not a legal requirement for owners of storage equipment to follow HSG76 guidance and SEMA Design Codes. However, if the HSE were to take enforcement action they would in all likelihood reference these documents, in conjunction with the aforementioned legislation, as a framework to bring action against your business. To adopt a safe culture, you need to be aware that racking follows a circular lifespan.
These are the key areas covered by HSG76 and SEMA advice:
- Racking design: As an engineered structure, the design of your racking must fulfil set criteria to ensure the structure is suitable for its intended purpose. HSG76 expects that “Racking systems should be of good mechanical construction, of sound material, adequate strength and installed and maintained in accordance with the manufacturer’s instructions”. To ensure racking meets these conditions, racking suppliers should work to design codes. These provide guidance to suppliers on how to do the structural analysis, the types of loads you must consider, how to test components and what factors of safety you require. In the UK, suppliers work to nationally recognised design codes such as the various SEMA codes or BS EN codes.
- Racking installation: HSG76 very clearly stipulates key considerations for the installation of your racking and states that “Racking should be erected on sound, level floors, capable of withstanding the point loading at each base plate. Aisles should also be wide enough to ensure that mechanical handling equipment can easily manoeuvre”. It also asks that “The racking should only be installed by competent people in accordance with the manufacturer’s instructions”. To help business owners meet HSG76 requirements, SEMA developed the Storage Equipment Installers Registration Scheme (SEIRS). This initiative aims to raise installation standards by instructing installers on correct and safe installation methods in line with SEMA standards. SEIRS is also referenced in HSG76.
- Racking usage: Once in place, the racking user is responsible for ensuring any damage on the storage equipment is recorded and actioned. HSG76 recognises that, in many cases, racking is manufactured from thin gauge high strength steels with a limit to the amount of abuse it can withstand. Any amount of damage to the racking can significantly reduce the load-bearing capacity and stability of the structure. To ensure the racking remains serviceable and safe, HSG76 follows SEMA guidance by recommending regular inspections. The inspection process starts with employees who work in areas with racking immediately reporting any issue with the structure. They should receive training on how to identify damage to the equipment and the correct steps to report the issues. This is followed up every week with a visual inspection undertaken by a member of your team which, in HSG76 is known as a ‘Person Responsible for Racking Safety (PRRS)’. They will check the use of the racking and that maximum loads are never exceeded. They will also identify and report any damage for action.
As referenced in HSG76, a rack safety awareness course is available through SEMA, which not only trains for the role of PRRS but ensures anyone working in areas with racking can identify and report damage. - Inspection: The inspection process is completed with the Expert Inspection. Carried out at intervals of no more than 12 months, HSG76 asks that the inspections are “carried out by a technically competent person”. The inspector should issue a detailed written report outlining observations, recommendations and proposals for any necessary remedial work. To support this, we operate our SEMA Approved Rack Inspector (SARI) initiative. This scheme consists of highly qualified professionals who must successfully pass an intensive three-day training course, written exam, and practical assessment to achieve their qualification.
Warehouse owners should be aware that there are two different types of inspection available. A “damage only” pallet racking inspection provides a list of damaged items and their location while a SARI report offers far more useful detail. To avoid inspectors who ‘claim’ to conduct SARI inspections, we always advise checking the credentials of your SARI inspector by asking to see their card.
HOW TO FIND A RACKING SUPPLIER
With so many areas to cover, it can be hard to know which racking supplier will ensure you are meeting your requirements, especially in an industry where there are few barriers to entry. A lot of the regulation now expects the owner of the racking to check the credentials of the company they work for – a timeconsuming process.
To provide a clear benchmark within the industry, SEMA set out to rigorously check the credentials of its members and provide reassurance for the market.
SEMA is made up of storage equipment manufacturers, suppliers, installers and inspectors who want to raise the standard of quality and safety within the industry. To join, each member must undergo a tough audit process which checks they meet HSE and industry requirements and show a commitment to using SEIRS racking installers and SARI inspectors.