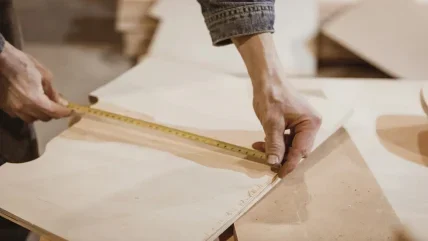
Members of the Timber Trade Federation and Plywood Club of London gathered for a unique double header recently to hear US plywood manufacturing expert Dick Baldwin.
Mr Baldwin has recently published the revised fourth edition of his book "Plywood and Veneer-based Products Manufacturing Practices".
"The plywood industry over the last 20 years has been through a once in a lifetime climatic change in which it has had to change from what it was to something different," said Mr Baldwin, owner of Oak Creek Investments.
"Plywood is dead, some people say. I say no!"
Up until about 2003, North America was the largest plywood-producing region in the world.
Now China is easily the largest with a 68% share of global production, against the US with 7.2%. The next largest regions are Indonesia on 3.9%; Malaysia (3%) Russia (2.5%), Brazil (1.9%), Canada (1.3%) and Finland (0.8%) – figures FAO of UN.
In 2013, about 134 million m3 of plywood were produced globally, with at least 100 countries engaged in plywood production, though eight countries accounted for 90% of global production.
Mr Baldwin said despite the onset of OSB, the financial crisis and other competitive pressures, the international plywood trade doubled to US$14.9bn in 2013 from US$7.4bn in 2003, putting paid to fears that plywood was on a perpetual downward path.
He said a major 15-year phase of plywood sector "turbulence and "reinvention"(1999-2014) had been characterised by globalisation; tree and process improvement; technology flexibility; new players and new producers; and consumption patterns.
Plywood producers have had to adapt to competitive realities, focusing on the unique characteristics of a veneer-based panel, solidifying around core strengths and automating at a faster pace.
He says plywood now comes from a renewable resource, with use of a wide variety of species.
And Mr Baldwin disputes the argument that plywood can be produced cheaper offshore. "I can get a better veneer out of a 10in diameter log than a big old growth log, as long as the tree is grown properly." Mr Baldwin said a key was for producers to turn problems into opportunities and use new raw materials.
"I believe plywood will recover from the onslaught of OSB," said Mr Baldwin.
"A modern plywood mill can use the same material as an OSB mill.
"But if you do not think you can compete, you probably won’t compete."
So what will be major barriers for plywood in the coming years?
Failing to be innovative enough to service customer needs and cost effectively manufacturing plywood to agreed upon specifications, he said.
In the years ahead, he sees continuing and growing challenges, including achieving housing goals and coping with government regulations on raw material and the conversion process.
"The further ‘survivor of the survivors’ will emerge from this process," he predicted.