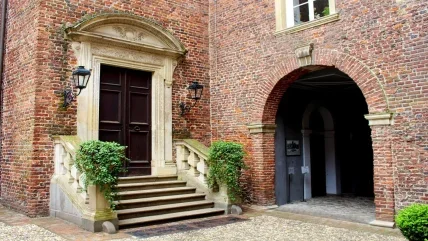
Summary
¦ The rising cost of all raw materials is squeezing margins.
¦ Public spending cuts and the rise in VAT could affect joinery demand.
¦ The RMI market continues to be steady.
The firmer, more consistent demand for joinery experienced late last year has continued into this, although no-one is breathing a sigh of relief quite yet.
In the mass market one leading producer said sales were ahead on 2009, with folding patio doors proving especially popular, and merchants’ interior door sales also doing well.
“Our sales are up and trending the right way,” said another contact, adding that although England’s early exit from the World Cup disappointed fans, it meant there would be less disruption in the building industry during the event.
Specialist joiners also report improved business. One said his company was “in a fitter state” than a year ago and demand over the past six months had replenished order books. “Our order intake is massively up and I have a strong feeling about our immediate prospects,” he said.
Fire door sales
It was a similar picture at another bespoke manufacturer. “We’re flat out,” he said, adding that the company had just added another shift on the paint line. Fire door sales were going well as local authorities upgraded their housing stock, he added, and there was also steady demand for windows and doorsets for new social housing.
“There has been more activity in the private new build sector which has stimulated demand for standard joinery products,” said another leading joinery manufacturer. “Equally, merchant sales have improved although the market is very competitive.”
One company cautioned people not to get carried away by comparing this year’s joinery trade with that in 2009, “the worst year in living memory”. “It’s probably more sensible to benchmark with 2008,” he said.
But with his perspective on the wider market, British Woodworking Federation chief executive Richard Lambert also agreed that joinery business was on a more even keel.
“It’s been pretty steady for most of this year,” he said. “It’s still tough and people are having to fight really hard to get the work, but the feeling is there’s still work out there.”
VAT concerns
One area of concern, however, was the impact of the upcoming VAT hike to 20%.
One source said that as the cut to 15% hadn’t had much effect, a rise of 2.5% wouldn’t either. “I don’t think it’s enough to stop people spending £20,000,” he said, but then added that some orders were being placed ahead of the increase next January.
Another producer was less sanguine about the rise. “It adds end user price pressure and on top of other issues will have an adverse effect,” he said. “Selective exemptions could have been a compromise, as with replacement windows and other energy-efficient products.”
“If the housing market suddenly stutters because everyone’s worried about VAT then we could be in the mire again,” said a fellow manufacturer.
What companies clearly believe could also upset market recovery are government spending cuts, with public housing and education building expected to be hard hit.
“In recent times these have been well invested and buoyant,” said a producer. “Cuts could hit specialist joinery providers to these areas particularly hard.”
Mr Lambert shared manufacturers’ fears. “Private housebuilding is beginning to pick up, but the big unknown question is what’s going to happen to the public sector. We know that capital spending will be cut by a third, but we won’t know until the spending review in the autumn how it will impact in terms of detailed programmes,” he said. “The public sector has propped up construction for the past two years, but if that spending is withdrawn before the private sector can cope, then the economy – and demand for joinery – could slip back again. And the construction industry is not out of recession yet.“
Rising costs
Joinery companies also raised the issue of rising raw materials prices and other overheads and how this was likely to affect demand and profits.
“The prices of timber and related components have been increasing and this trend will continue,” said a manufacturer. “Added costs will be passed on, unavoidably, at least at list price so there will continue to be competition and discounting on prime products.”
While demand may have picked up, other joinery companies said customers were still pressing for deals. “A lot of people are driving very hard bargains, so prices are still under pressure and margins tight,” said Mr Lambert.
Another contact said he was having to pass on higher timber prices, but that they were being offset to some extent by the better euro/sterling exchange rate.
Generally, UK joinery producers say they are still more upbeat, certainly than they were last year. But as one said, they’re aware the industry is “not out of the woods yet”.
“Things appeared to have stabilised but there’s now some concern for growth following the budget and the repercussions from it directly and indirectly on spending levels, investment and interest rates,” said a manufacturer.
Another said what was now needed to underpin recent market improvement “was something to ensure we keep building houses”. “They should put interest rates up a bit so banks want to lend money again and get things moving,” he said.