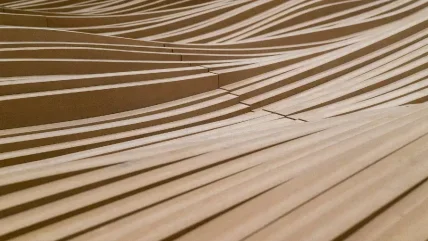
Summary
• MFC sales have been better than raw board and T&G sales.
• Increases in producers’ costs have slowed.
• Sonae’s Knowsley factory is running at 90-95% capacity.
• Germany was the leading overseas supplier to the UK last year.
Experts are divided in their analysis of the UK chipboard market, with some key players claiming to have enjoyed a stronger than expected first quarter in terms of sales while others have been disappointed in the volumes they have been able to move.
Without doubt, this divergence of opinion owes something to the relative strengths of the different product groups; broadly speaking, sales of melamine-faced chipboard seem to have been better than those of raw board and T&G.
Meanwhile, the first quarter brought few movements in domestic chipboard prices; indeed, one major player contacted this week bemoaned the “less than unified approach” in domestic producer circles towards pushing for much-needed upward price progress.
Production levels
Over recent months, a key factor in the domestic chipboard market has been Sonae UK’s return to production at its Knowsley facility following the serious fire in June last year. A senior spokesperson confirmed in early April that, having restarted production in mid-December, the facility is now producing typically at 90-95% of its capacity. “We are where we said we were going to be with regard to output,” he said. The company is now involved in detailed applications for the second phase of this programme, covering a reconfiguration of the particle preparation and wood storage area.
According to the spokesperson, the company’s attempts to increase its chipboard prices in early March had met with resistance from customers – attributing this to a combination of “competitor actions” and a softening of the market. He expressed disappointment at the lack of scope at present for implementing relatively modest increases in selling prices, saying there was no reason to fear that a much-needed injection of value into UK-made chipboard would result in business being lost to imported board.
Even though cost escalation “had not been as dramatic as feared” in the first quarter of 2012, he added that the underlying trend was still very much upwards, highlighting in particular the pressure coming from hauliers for an increase in their rates. Resin costs remained “volatile” and the pressure on recycled timber costs had intensified following Sonae UK’s return to production, a competitor said.
A senior spokesperson for another of the domestic chipboard producers agreed that the upward curve in some of his company’s costs had flattened of late; he put resin costs in this category but said that these were likely to gather momentum again sooner rather than later. Meanwhile, the impact of biomass had continued to push timber costs higher, while the paper for surfacing products had been rendered significantly more expensive by the rising costs of titanium dioxide, he pointed out.
Better than anticipated
However, he was considerably more upbeat about current market conditions, describing chipboard orders in the first quarter as “a lot stronger than we had anticipated” and hailing March as “one of the company’s strongest sales months ever”. During February and March, he continued, the company had introduced price increases of typically 3-5% on some products in the distribution market arena, including standard board. Another round of increases might be a possibility by the end of the summer/early autumn, he added.
Among many customers, widespread pessimism had given way to “a little bit of optimism”, he said. “We are hearing some good news out of some of the major builders, particularly in the south of England,” he added. At the same time, major retailers had committed to substantial store refurbishment programmes while activity in the social housing sector had developed a decent rhythm, he said.
The company had continued to produce chipboard over Christmas and New Year but demand in the first quarter had been sufficiently strong to ensure a return to “normal” stock levels. The business was budgeting for 5-10% volume growth in chipboard this year, he said.
However, another producer contended that “distributors, merchants and industrial customers are all saying it is quieter than they had thought it would be” during the first quarter, adding that many of them appeared particularly nervous about the potential for the Easter break to cause significant disruption to business flows.
Raw board market
Balancing both of these views, a domestic competitor said the raw board and T&G markets had become relatively “dull” in March and early April following a bright start to the year, whereas demand for MFC remained robust. Overall, he said, chipboard sales volumes in the first quarter had been broadly in line with those of the corresponding period last year. He added that he wasn’t planning a price increase for chipboard at the moment.
In its most recent financial statement, Norbord confirmed that its chipboard prices in Europe “firmed rapidly” throughout 2011, gaining 15% across the year as a reflection of the need to recover higher raw material input costs; the group’s European chipboard production volumes climbed 2% last year, it added. A senior figure for another UK chipboard producer estimated that the product had achieved a total price increase of nearer 20% during the course of 2011, before adding that the pace of price increases was not as strong as it had been 12 months ago and that these were now “more inflation-related”.
Meanwhile, latest figures from the Timber Trade Federation (TTF) reveal that UK exports of chipboard declined sharply last year: totalling 121,000m³ in 2011 as a whole, overseas shipments were 15.6% below the 143,000m³ exported in 2010; for additional context, however, it should be remembered that UK exports were a massive 27.4% higher in 2010 than they had been in the previous year.
At present, said a UK producer, chipboard export opportunities are “quite strong”, with some “nice volumes” sold recently to Continental Europe at “comparably good prices” when viewed alongside returns from domestic sales.
UK imports
UK chipboard import statistics released by the TTF show that volumes arriving on these shores climbed 7.7% from 453,000m³ in 2010 to 488,000m³ last year. However, this upturn owes much to the fact that Sonae UK brought in substantial volumes from elsewhere within the group in order to protect continuity of service in the aftermath of the afore-mentioned fire at Knowsley last June. Chipboard volumes from Portugal soared more than 38,000m³ last year to increase the country’s share of the UK import market from 4% in 2010 to 12% in 2011.
The stats also confirm that Germany was the UK’s leading overseas supplier of chipboard in 2011, raising its shipments by some 27,000m³ to boost market share from 28% to 32%. And despite upping its deliveries to the UK by approaching 10,000m³ last year, France’s share of total UK imports remained unaltered at 29%.
As regards the outlook for 2012, several producer contacts spoke of their cautious optimism. However, one of them captured the general mood by saying: “I don’t expect a big upturn in the market but, rather, continuous improvement in small steps.”
If investment in the business represents the most tangible indicator of confidence in the future, then the outlook certainly seems positive to Egger UK. The company invested a total of around £25m in its UK operations last year and has committed £9m to a new lamination line at its Hexham base that will initially add around 10% to its existing laminating capacity; the first board is expected to come off the line before the end of April. In addition, Egger UK has spent around £700,000 on the relaunch after some five years of its service-based Zoom decorative product offer. And as noted recently, Kronospan is investing £5.5m in a melamine embossing line at its Chirk plant, with production scheduled to start in August this year.